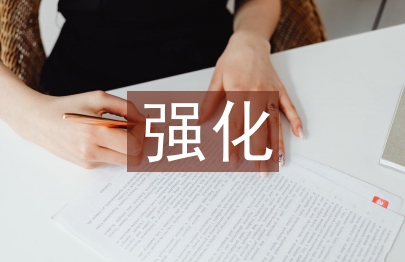
1.低热值煤气中心烧嘴TGS石灰窑主要特点
1.1节能
TGS石灰窑之所以节能,首先是因为采用六段式哑铃形炉型,这是结合高炉炉型结构,经过多年生产实践摸索而成。唐山今实达科贸有限公司(以下简称我们)通过提高炉身高度,优化炉型和高径比,延长了预热和冷却时间,此炉型特别适应石灰导热系数低和石灰焙烧的特点,降低了出料和炉顶废气温度,从而达到节能的效果。其次,TGS石灰窑采用了余热回收装置,助燃风可预热到180~260℃,我们还增设了煤气换热器,煤气可预热到150~200℃,实现了双预热,有效提高了石灰窑的热效率,达到非常好的节能效果。目前全高炉煤气TGS600石灰窑热耗为870~980kcal/kg,吨灰高炉煤气消耗量低于1300m3,实现了利用低热值煤气(全高炉煤气、转炉煤气、发生炉煤气或混合煤气)焙烧石灰的节能目标。
1.2环保
窑体部分主要扬尘点有2处:一处是小车倒料点,另一处是排料点。小车倒料点我们采取的是全密封和抽风除尘,保障了粉尘不外扬;窑底排料点采用双道液压密封阀,此装置借鉴了高炉炉顶料罐上下密封阀的原理,减少窑底粉尘污染,改善劳动环境。除了窑体的这两个扬尘点之外,窑体废气量也影响着环保效果和投资。由于TGS石灰窑热效率高、节能,助燃风与煤气使用量小,所以废气量也少,环保投资低、环保设备运行费用低、易达标。成品石灰处理系统,采用料仓,避免了石灰落地和铲车处理,并加强了密封,减少了扬尘量,特别是用低振幅密封分级筛,可以在密封的状态下把石灰筛分出3个品种(炼钢灰,LF炉灰和破碎成烧结灰),此处很少抽风量甚至不用抽风除尘也不产生扬尘。并且配备了脉冲引射反吹布袋除尘器,既可把排放降到10mg/m3以下,又提高了布袋寿命,节省了压缩风,且维护保养方便,进一步节省了环保运行成本。
1.3降低吨钢灰耗和炼钢成本
TGS石灰窑为了提高生产指标,主要做了如下几方面的工作:1)炉顶布料采用空转螺旋布料器,借鉴了现代大型高炉上旋转布料器的布料思想,在提高布料均匀性的同时调节整体气流分布。保障了大型TGS石灰窑的产量和质量的稳定。2)窑底排料设备采用的液压往复出料机与双道液压密封阀配合出灰。既可全炉均匀排料,又可单点调节排料量,出灰量和时间间隔由操作专家软件控制,实现了吨灰恒热量焙烧,炉内实现炉墙边沿炉料与中心炉料全断面均匀下料,防止出现抽心现象,经过我们生产中排料试验检测下料的不均匀程度在1.5%以内,保障大型TGS石灰窑高产和顺行,也减少了生过烧。3)TGS石灰窑采用大型风冷中心复合烧嘴,煤气和助燃风分别通过炉外调节,进行合理配比,中心烧嘴顶部环形布置的烧嘴自内向外烧。炉墙布置的国井式侧烧嘴自外向内烧,内外烧嘴实现了对烧,燃烧稳定,寿命长且不易回火,火焰穿透能力是传统石灰窑烧嘴的1.4倍以上。每排烧嘴分别设置了一套温度自动控制系统,通过自动调节功能使燃烧温度稳定在设定的目标温度范围内。中心烧嘴与国井式侧烧嘴配合对烧,提供了充足的中心火焰,解决了石灰窑中心气流不足、温度分布不均、中心生烧和边缘过烧的问题,使石灰窑的气流、温度分布更均匀,并可及时调节,提高了产量和产品质量。4)自动化系统配备专家系统软件,当专家软件设定好参数后,TGS石灰窑即可实现自动排料、自动上料和恒热量自动燃烧。整个操作控制系统简单易掌握,并能检测窑内下料是否偏行,气流分布是否均匀,还可对工长每次操作的效果是否到位、有无负作用,加以提醒和警告。TGS石灰窑气流分布均匀、温度分布均匀、布料均匀、排料均匀、自动化控制强,以TGS石灰窑生产烧结灰和炼钢灰后,保障了石灰的产量和质量,为生产低硅低硫生铁、降低吨钢灰耗和炼钢成本打下了坚实的基础。
1.4生产成本低
TGS480石灰窑生产成本低,主要体现在以下几个方面:1)热利用率高。用全高炉煤气时(含30~45℃饱和水,高炉煤气热值680~750kcal/m3),热耗为870~980kcal/kg,节省燃气。2)TGS石灰窑产量大、密封性好,在粉尘排放下低于10mg/m3的高标准下,吨灰环保设备功率低,节省用电量。3)中心烧嘴和侧烧嘴等炉体非标设备使用寿命长,维修费用低,吨灰维修费仅为2.5~4.5元/t。4)整体石灰窑工程投资低,折旧费用低。5)机械化自动化程度高,节省了人力费用。
1.5安全
TGS石灰窑的主要安全措施如下:1)完善的自动燃烧控制和煤气安全联锁控制。这主要体现在煤气压力超出控制、突然停电、风机等关键设备突然停机等等一些状况,不靠人员操作,我们的自动化系统可以保障即时自动切断煤气供应,自动完成安全停炉作业,同时实现自动充氮吹扫。充分保障现场人员及设备的安全。2)在供料系统、排料系统和成品处理系统的各个设备中均设有完善的事故连锁停机控制功能。3)在各个有可能煤气泄漏的区域,均设置煤气监测及报警系统,每班配备袖珍式煤气监测仪。
1.6适应能力强
TGS石灰窑适应能力强,主要体现在如下几个方面:1)适用多种燃料。高炉煤气、转炉煤气、发生炉煤气、混合煤气、焦炉煤气。2)TGS石灰窑还可以配备气煤混烧设施,在长期煤气不足情况下,仍可以满负荷生产,甚至全煤烧生产。3)当石灰石质量较差时,TGS石灰窑的能耗、产量、质量相对其他窑型变化较小。4)生产弹性大。TGS石灰窑可根据用户的需求降低或增加产能。设计能力在一定范围内调整,石灰的质量不受影响,石灰窑生产稳定。
2.下料过程分析
2.1TGS石灰窑的下料理论
由于石灰石刚分解为石灰时,其石灰石晶格结构遭到巨大破坏,晶体内部存在大量微孔和空位,比表面积巨大,此时遇水就会爆炸,其活性度是很高的,这就说明刚产生的石灰发生再结晶和黏结是必然的,问题是要把石灰的再结晶发育程度和黏结控制在允许的范围内,从而保障石灰的活性度和防止黏结。而影响石灰再结晶发育程度的关键因素是温度和在此温度下的持续时间,且两者是相互关联的,对于每一种石灰石的成分和原始结晶状态,石灰再结晶发育程度呈现复杂的关联关系,对于黏结或结瘤的发育程度也有类似的规律,更重要的是黏结只发生在两个石灰块的持续接触面上,因此黏结的发育过程比再结晶还要来得缓慢一点。对于黏结问题需要从竖炉下料过程做进一步的分析,以便加以解决。
2.2TGS石灰窑的下料过程(通俗称为拱桥现象)
包括高炉、石灰窑、球团竖炉等,对于几乎所有的块状物料高温竖式窑炉,炉内(块状带)块状物料到底是如何下料的,在竖炉生产特别关键的中下部和高温区块状带内,由于物料下方的机械或物理化学作用,形成了多个尺寸不同、位置不同的局部小空间(或形象称为亚稳态悬拱空穴),每个小空间的顶部块状物料,在上部和周围块状物料的挤压、摩擦、粘结作用下,形成了拱桥结构,这种亚稳态悬拱空穴(有点类似不规则椭球结构,与液体中气泡的有些状态类似),对竖炉的气流分布(孔隙率分布)和下料都产生了至关重要的影响。这些小空间的尺寸与炉况具有对应的统计规律关系,从约0.1个料块到几个料块尺寸,甚至几十个料块尺寸都有,极限悬料时为接近炉子内径尺寸;一般正常炉况时,几率比较大的小空间尺寸约为0.1~6个料块尺寸,炉子中下部和高温区以0.1~4个料块尺寸,炉子上部以约0.1~2个料块尺寸较多,越向炉身高处,小空间的尺寸越小且多,分布也越均匀;炉况越顺行,小空间的尺寸越小且多,分布也越均匀。通俗地说,竖炉内块状物料的下料过程:大部分时间内,上述的小空间的拱桥是亚稳定的,整个炉料料柱的有效重量始终是向下且大于零的,此时附近(其上和周围)的炉料处于相对静止状态,在料块之间的微小接触面上黏结这一物理化学过程开始发育;突然,某种机械或物理化学作用导致了该拱桥的桥墩或桥拱崩塌,则其上和周围的物料在瞬间塌落,并占据了该小空间,而在其上方的某个高度,该小空间可能又稳定住了(也有时分裂为2个或多个或与别的小空间合并成1个大一点的小空间),就像一个小气泡连续上升或又停止一样,正是这些小空间(或形象称为亚稳态悬拱空穴)不稳定的、间断的、随机的,又有一定物理化学、力学原理和统计规律的塌落运动,表达了竖炉内高温区块状物料下料规律的主要特征。在这个瞬间塌落过程中,产生了一定的冲击力、扭转力和摩擦力,如果在此之前的黏结过程发育得不是太严重(与温度和持续接触时间关联),其黏结强度就不是太高,此时就可以被掰开,而后新的黏结过程又重新开始了,进入良性循环,这就是我们通常所说的“没有黏结”的正常下料过程。竖炉块状物料的下料过程就是尺寸不等、分布也有一定统计规律的亚稳定小空间拱桥随机的、不稳定的:拱—塌—拱—塌—拱—塌的过程,而每一次小空间(形象称为亚稳态悬拱空穴)拱桥稳定存在的时间,就是其上和附近物料料块之间的持续接触时间,正是这个持续接触时间与温度、炉料成分、粉尘成分和含量等决定了黏结块是否能够保留下来,同时粘结本身也增加了拱桥的桥墩或桥拱的稳定性(对于下料是不利因素),并且方向向下的有效重始终存在,正是这个有效重力扮演了一个双重角色:由此导致的料块之间的挤压力、摩擦力,稳定了拱桥,并加剧了黏结,对下料是不利的;而拱桥崩塌瞬间,也是这个有效重力使料块下落;多数情况或正常炉况下,加大有效重对于下料是不利的,同一高炉在轻负荷、或高冶炼强度、或喷煤后(压差升高)的情况下,高炉下料反而改善,正说明了这个问题。这是本文的下料过程分析与高炉有效重下料理论的本质区别,也是高炉近些年进一步强化冶炼的依据。对应在炉内高温区的黏结过程:黏—掰—黏—掰—黏—掰。一旦温度过高或小空间拱桥的稳定时间过长,就会导致料块与料块之间的持续接触时间过长,黏结过程就发育得太厉害了,其黏结强度就太高了,在上述的塌落过程中也掰不开了,黏结块就被保留了下来,而黏结块一旦被保留下来,它会进一步影响气流分布和温度分布,也会使它参入的新的拱桥更稳定,尺寸也更大,这样自动提高了局部的温度,也进一步延长了拱桥稳定存在的时间,即进一步延长了料块与料块之间的持续接触时间,由此导致新的黏结块的大量形成和已有黏结块的快速长大,进入恶性循环,这就是我们通常所说的黏结或结瘤(也必然伴随着下料不匀)。炉况越顺行,小空间(形象称为亚稳态悬拱空穴)的尺寸越小且多,分布也越均匀,使炉况更容易保持在良性循环中(产量更高、能耗更低、质量更好,对突发问题抵抗能力增大);炉温过高、下料时间间隔过长、每次下料过少,产量过小、有黏结块或结瘤等情况下,这些小空间(形象称为亚稳态悬拱空穴)的尺寸明显变大,且分布更加不均,这就是下料恶化的主要原因。另外排料不匀、布料不匀、气流不匀、温度不匀等也是通过上述机理造成了炉内料柱下料不匀的,而这些小空间分布规律的恶化,又会反过来加剧气流不匀、温度不匀和粘结或结瘤,从而形成恶性循环。
3.TGS石灰窑的设计与生产操作
1)采用六段式哑铃形高炉身炉型,并配备相应的压力,以此提高有效容积利用系数和节能,这就加快了竖炉单位有效截面积的物料流量和气体流速,加快了料流速度,提高了料柱的空隙率(即料柱的透气性),缩短了拱桥稳定存在的时间,也就是缩短了料块与料块之间的持续接触时间,由此保障每次拱桥塌落可以掰开黏结块,同时也保障了石灰活性度在330mL以上。2)排料时间间隔缩短到15min以内。开炉或调整炉况时,可人为增加一点生烧,也不降低排料速度。3)煤气不足时,多台炉的工厂可停产1座炉子,留出充足煤气保障其他炉子的满负荷生产。因为炉子低负荷生产的总CaO少,还容易结块或结瘤。4)刚停炉时,石灰窑2h内必须继续排料活动料柱,逐步减少排料量,而球团竖炉的活动料柱时间要延长至5h以上,而更长时间的停炉,每班也须活动料柱2次以上。
4.结语
竖式窑炉、高炉、球团竖炉、耐火材料熟料焙烧炉、石灰窑等行业的节能、减排,提高质量,降低成本,低热值煤气中心烧嘴TGS石灰窑的生产实践和用拱桥现象进行下料分析为行业的发展提供了一些新的思路,这些对竖式窑炉的设计改进与生产操作的提升有很大帮助。