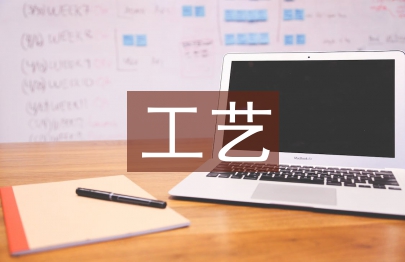
脱硫工艺论文篇1
过程:用电石泥作固硫剂,煤泥经刮板机进入下仓,在下仓投入电石泥,与煤泥按一定比例混掺,由预压螺旋送至搅拌仓,再次搅拌均匀后由浓料泵送至锅炉本体内进行燃烧,达到固硫的效果。
优点:炉外脱硫设施前SO2浓度可以降至500-800mg/m3,电石泥的固硫率在30%左右。
无需添加任何其他设备即可进行,节约成本及设备投入。
炉内固硫过程示意图
2.炉外脱硫:
过程:整个炉外脱硫系统主要由脱硫剂制备系统、吸收循环系统、副产物处理系统、配电及自动控制系统四大部分组成。
电石泥投入化灰池,清水泵开启注入清水,然后进入搅拌池,搅拌均匀使之与水充分混合,制备成为电石浆液。加浆泵经管道将浆液送至脱硫塔。首先烟气与浆液直接接触脱硫,然后4台浆液循环泵分别将电石浆液打入脱硫塔上部的喷淋装置,电石浆液经雾化后再次与烟气中的SO2反应,进一步除去烟气中的SO2。脱硫过程中所产生的未氧化的亚硝酸钙(CaSO3•1/2H2O)与自然氧化产物石膏(CaSO4•2H2O)的混合物经排渣系统排至沉灰池。
优点:整个脱硫系统位于烟道末端,除尘系统后,其脱硫过程的反应温度适中;
湿法烟气脱硫反应是气液反应,脱硫反应速度快,脱硫效率高,钙利用率高;
系统可利用率高、运行费用低、维护简单、运行人员少、能确保人员和设备的安全、能有效地节约和合理利用能源;
系统位于锅炉引风机之后,且有旁通烟道,脱硫系统相对独立,运行不会影响主体设施,且维护检修方便;
炉外脱硫过程示意图
2电石泥脱硫机理
在燃烧过程中,燃煤中的硫可以分为有机硫和黄铁矿硫两大部分,硫分在加热时析出,如果环境中的氧浓度较高,则大部分被氧化为SO2而很少部分残存于炉渣中。电石泥的主要成分是Ca(OH)2。
1.反应机理
Ca(OH)2+SO2=CaSO3.1/2H2O+1/2H2O
CaSO3.1/2H2O+3/2H2O+1/2O2=CaSO4+H2O
影响循环流化床锅炉脱硫效率的主要影响因素:(1)Ca、S摩尔比的影响。Ca、S摩尔比被认为是影响脱硫效率和SO2排放的首要因素,根据试验表明,Ca、S摩尔比为1.5~2.5时,脱硫效率最高,而继续增加Ca、S摩尔比或脱硫剂量时,脱硫效率增加的较小,而且继续增加脱硫剂的投入量会带来其他副作用,如增加物理热损失,影响燃烧工况等。(2)床温的影响。床温的影响主要在于改变了脱硫剂的反应速度、固体产物分布。从而影响脱硫效率和脱硫剂的利用率。有关文献表明,床温控制在850~900℃时,能够达到较高的脱硫效率。(3)脱硫剂粒度的影响。
2.计算用量
根据电石泥脱硫理论,按照给煤含硫量1.6%,Ca、S摩尔比2.5,电石渣中含水、杂质比例45%(其中含水40%,杂质5%),其余成分Ca(OH)2,07年我厂全年总耗煤约为耗煤量104253吨量计算,
(Ca的摩尔质量40,O的摩尔质量16,H的摩尔质量1)
进行理论计算
我厂每年产S量:104253×1.6%=1668.048(吨)
每年需Ca量:2.5×40×1668.048/32=5212.65(吨)
每年需Ca(OH)2量:(5212.65/40)×74=9643.4025(吨)
理论需要消耗电石泥量:9643.4025/(65%)=14836(吨)
3.脱硫试验
为了验证脱硫效果,对加电石渣进行脱硫加以记录(一小时中4次记录值)
4.数据分析
按照一定的比例加入电石泥,脱硫效率可以达到90%,能够将二氧化硫的排放浓度降到国家环保要求的480mg/m3以下。
5.存在问题
由于煤泥中搅拌添加电石泥,添加比例不好控制,搅拌不均匀,导致煤泥打空,容易出现个别点排放量超标。
6.建议
增加电石泥给料和输送设备,确保掺烧比例及掺烧均匀。
3结论
(l)我厂采用炉内掺烧脱硫剂(电石泥)固硫,和炉外烟气脱硫FGD湿法脱硫相结合的二段式脱硫方式脱硫取得成功,脱硫效果能够达到国家环保要求。
(2)按照每年用煤炭10万t计算,可以消耗近1.4万t电石废渣。不仅减少了这些废渣对环境的污染,而且为以废治废开辟了新的途径。
(3)利用废电石渣作为脱硫剂,不再采购石灰石大大地节省了运行费用。
(4)系统维护简单、运行人员少、能确保人员和设备的安全。
4参考文献
《电石渣干粉在电厂烟气脱硫工艺中的应用》---作者:史红
《燃煤炉预混—喷钙二段脱硫技术研究》------作者:刘建忠,周俊虎,程军,曹欣玉赵翔,岑可法
脱硫工艺论文篇2
0 引言
我国煤炭资源虽然丰富,但焦煤资源只占查明资源储量的27%,可采储量只有700亿吨。目前国内焦炉生产规模已达7亿吨,2012年焦炭产量超过4亿吨,耗原煤8亿吨左右。根据国内主要矿区炼焦用原煤工业分析看,在炼焦煤采出量(占可储量的50%)的原煤中,硫份超过1.5%的炼焦用煤超过25%,因为配煤中硫含量高,造成焦炭质量下降,生产成本上升,从高硫炼焦煤矿区煤层原煤含量分布特征分析,国内炼焦煤硫份以年轻的低变质的气煤和1/3焦煤最低(1%以下),而变质程度较高的年老气煤、肥煤和焦煤含硫份相对较高,(大于1%)从成份硫分布比例分析,绝大多数矿区的高硫煤的成份硫都以硫铁矿(Sp,d)为主,一般占全硫(St,d)的50%—80%。有机硫(So,d)一般占全硫的15%-40%,通常以硫铁矿为主的煤经洗选后精煤硫份会有较大幅度降低。以有机硫为主的高硫煤,洗选后精煤硫份比原煤更高。有机硫是煤分子的一部分,主要以脂基硫、芳基硫、噻吩类硫分布于煤分子中,因此脱除难度很大。
焦煤中的硫份只有30%-50%经裂解进入煤气中,大部分硫残留在焦炭中,根据硫份在焦炭中的位置,可将脱硫技术分为入炉前脱硫,焦化过程脱硫和煤气脱硫三个阶段过程,本文分别进行技术分析和论述。
1 焦煤入焦炉前脱硫
1.1 无机硫的脱除 无机硫脱除一般以物理法为主,它主要以硫铁矿和硫酸盐的形态存在于煤的夹层中,以地质结合为主,由于国内原煤洗选工艺一般以脱灰为主,原煤中无机硫的脱除率一般在40%左右,如将原煤洗选粒度降至一定程度,硫铁矿的脱除率可大幅提高,因此只要将部分洗煤设备和工艺加以改进,即可有效的提高无机硫的脱除效率,目前,国内外已有成熟的设备,通过优化洗选工艺,脱除原煤中的硫铁矿。它工艺可靠,脱除效率高、投资省、运行成本低,已得到洗煤行业的高度重视,一些专业的洗煤厂商已将脱除无机硫做为设计重点,主要采用重力法、浮选法、磁选法等几种工艺。
重力法是按煤和硫铁矿比重差异进行脱硫,这是目前焦煤脱硫的主要手段,使用重介质旋流器可以实现低密度,高精度的分选,分选粒度下限可以达到0.1-0.2mm,能有效地排除未充分解离的中间密度的硫铁矿与煤的连生体,而获得较高回收率的低灰低硫精煤,高密度的硫铁矿使用重介工艺可使煤与硫铁矿进行有效的分离,且脱除率较高。
浮选法主要处理重介质分选粒度下限微未级的细微粒煤,上限可以达到0.3mm以上,弥补了重介质分选的粒度范围,在该粒度状况下,煤与硫铁矿连生体已基本被分离,只要选用合适的浮选制,利用颗粒表面润湿差异和空气微泡有条件吸附而形成的表面张力就能有效的分离出硫铁矿和灰分,微泡浮选柱具有明显的去硫除灰能力,而且对微末级的极细粒煤效果非常好。
磁选法主要利用硫铁矿自身的磁性对其进行脱硫,它是根据煤效组份与硫铁矿的磁性差异进行脱硫。它是浮选法的工艺补充,主要针对0.3mm以下的泥煤中的硫铁矿,但因硫铁矿磁性较小,虽然显顺磁性的,需专用的磁选机和较复杂的流程,因此国内洗选厂家选用有限。
1.2 有机硫脱除 有机硫的脱除是一个复杂的氧化还原过程,一般的工艺条件很难有效的脱除,目前,理论上论证、试验较多的工艺有:氧化法、硝化法、氯解法、热解法,碱液法等多种化学脱硫方法,且综合脱硫效率能达到20-60%。如:利用浓氨水渗透打断与煤分子的有机结合健,再经过洗选分离出无机硫;利用热碱液浸泡焦煤8个小时以上(需加热进行恒温),生成硫代硫酸盐再分离;在密封容器中和一定的高温、高压条件下,加入空气氧化煤中有机硫;用NO2有选择性的氧化煤中的硫分,并以热碱液(Na2Co3和Ca(OH)2水溶液)处理后水洗;氯乙稀液萃取煤中硫组份;高温加氢法等。虽然化学脱硫方法较多,且脱硫效率也较高。但装置投资大,生产费用高,处理煤量规模小,易造成二次污染,生产条件要求高等弊端,很难规模化生产,只能用于超净化煤的处理。但有机硫含量高的原煤,一般含灰量较低,价格也偏低,可做为煤焦的配煤,控制焦炭中的总硫和总灰份。
脱硫工艺论文篇3
1除尘工艺
1.1选用原则
燃煤锅炉燃烧过程中产生的烟气是由黑烟和飞尘构成的。其中,黑烟是煤受热分解而成的微小碳颗粒在炉膛内未完全燃烧形成的,而飞尘则是由灰颗粒和部分未燃尽的焦炭细颗粒组成。QXL23吨燃煤锅炉构造较为完善,在正常情况下,燃烧工况较好,所以其排烟以飞尘(>5?m)为主要成分,其烟气出口烟尘浓度一般在2000mg/m3―5000 mg/m3,所以,选用多管陶瓷除尘器处理工艺。
1.2基础参数
基础参数见表1.锅炉出口SO2质量浓度按煤含量的1.5%计算,多管陶瓷除尘器出口烟尘质量浓度按除尘效率90%计算。
1.3湿式脱硫除尘器
工作温度t≤200℃,烟气处理量Q≤57700 m3/h,烟气阻力P≤1000Pa,除尘效率≥90%,脱硫效率≥70%。
1.4脱硫工艺
根据国家环保总局文件(环发【2002】26号《燃煤二氧化碳排放污染防治技术标准》的要求,综合考虑本单位的建设用地面积、脱硫剂的来源、脱硫后产物的消化处理,治理目标,在比较各种脱硫工艺后,决定采用双碱法脱硫工艺,具体流程为:锅炉的烟气进入脱硫除尘设备后,先经多个特制的喷头逆向喷向来自锅炉的烟气,使烟气与除尘器的水面没有接触前就与脱硫液进行较好的结合,同时脱硫液与烟气中的二氧化硫进行充分反应,除掉烟气中大部分SO2,经过进一步反应,烟气与脱硫液接触并冲击水面,将脱硫液雾化成直径0.1-1.0mm的液滴,形成良好的雾化吸收区。烟气与脱硫液在雾化区充分接触反应,完成烟气的脱硫和进一步除尘,经脱硫除尘的烟气向上通过除尘器的出风口直接进入风机并由烟囱排放到大气中。
众所周知,除尘是从烟气中分离颗粒物质的物理过程,而脱硫则是涉及气液传质和化学反应吸收过程,即烟气中二氧化硫的脱硫过程分两部分完成:1)气液传质和水合过程,即烟气中的二氧化硫与水接触时,溶解在水中,并与水反应生成亚硫酸;2)硫酸与溶解在水中的碱性脱硫剂作用生成亚硫酸盐。
以上三式视吸收液酸碱度不同而异,碱性较高(PH值>9)以(2)为主要反应;碱性略有降低时以(1)式为主要反应;碱性到中性甚至酸性时(5
2.应用效果
我公司两台锅炉经过技术改造后,气液在雾化反应区得到了充分接触并延长了反应时间,提高了吸收效果。对两台锅炉烟气脱硫除尘系统效果进行了对比(表2),脱硫除尘效果明显,达到了国家排放标准。
3.结论
(1)本除尘与脱硫工艺的理论分析是可行的,工艺改造是合理的,且结构简单,使用方便。
(2)本改造工艺应用于QXL23吨燃煤锅炉,但是对其它锅炉也有借鉴作用,经过一年多的运行,效果非常可靠,达到了改造的预期目的,且运行成本低,非常适合在油田注汽锅炉中推广使用。
脱硫工艺论文篇4
②Chongqing Institute of Environmental Science,Chongqing 401147,China)
摘要: 本文以某2×350M电厂(电厂A)为例,针对重庆地区高硫煤的特点,使用层次分析法为循环流化床锅炉选择一个合理的炉外脱硫工艺,使之与炉内脱硫相结合,组成一个两级脱硫工艺,以使电厂排气筒出口二氧化硫的浓度符合国家和地方的排放标准。
Abstract: Taking a 2 x 350 M power plant (power plants A) as an example, aiming at the characteristics of high sulfur coal in Chongqing area, this paper uses analytic hierarchy process to choose a reasonable outside-furnace desulphurizing process for circulating fluidized bed boiler to make it combine with desulphurization and compose a two-grade process, in order to make the concentration of sulfur dioxide eliminated from power plant pump export meet the state and local discharge standards.
关键词: 循环流化床锅炉 层次分析法 综合评价 二级脱硫
Key words: circulating fluidized bed boiler;analytic hierarchy process (AHP);comprehensive evaluation;two-stage desulfurization
中图分类号:TM621.2文献标识码:A文章编号:1006-4311(2011)29-0065-02
0引言
燃烧含硫率为3.92%(电厂A)的发电厂,如果仅仅使用循环流化床炉内固硫,则无论如何改变反应条件,甚至牺牲部分热效率来提高脱硫效率,也不能达到排放标准。本文试图运用层次分析法实现定量和定性分析相结合,避开实际情况中由于未定量带来的判断困难,为选择合适的脱硫工艺提供决策方法。
1研究对象
电厂A循环流化床锅炉拟燃用松藻矿区的煤矸石和劣质煤,设计煤种的收到基硫(St,ar)为3.92%,收到基恒容低位发热量(Qnet,var)为11.8MJ/kg。电厂A设计两台1162t/h的锅炉,经计算,在炉内固硫效率为85%时,排气筒出口烟气中SO2浓度未达标排放,因此,必须再选择一个脱硫工艺使之技术经济可行。
2工艺选择模型建立
2.1 工艺选择本次选择以下五种FGD[1,2]技术作为备选工艺:A:石灰石/石膏湿法;B:旋转喷雾干燥法(SDA法);C:CFB-FGD半干法;D:炉内喷钙尾部增湿(LIFAC法);E:电子束法。其中:A主要参考了重庆华能珞璜电厂一二期的脱硫设备的技术参数;B主要参考了山东黄岛电厂的脱硫设备的技术参数;C主要参考了四川内江发电总厂高坝电厂的脱硫设备的技术参数;D主要参考了南京下关电厂的脱硫设备的技术参数;E主要参考了四川成都热电厂的脱硫设备的技术参数。
2.2 层次分析法原理及步骤层次分析法[3](AHP)是美国匹茨堡大学T.L.Saaty提出的一种用于解决多目标复杂问题的定性与定量结合的决策分析方法。层次分析法共分为三步:第一步,将问题分解成不同的组成因素,按照各因子之间的相互影响和隶属关系将其分层,形成一个有层次结构的模型。第二步,对模型中每一层次因子的相对重要性给与权重值。第三步,通过计算各层次的组合权重值,得到方案层相对于总目标的排序权重值,以此作为方案选择的依据。
2.3 综合评价指标体系的提出综合考虑FGD技术自身特点,通过专家讨论、问卷调查等方式提出燃煤电厂烟气脱硫技术综合评价指标体系,其层次结构[4]如图1所示:
2.4 指标权重的确定本次采取大样本专家数量的主观赋值法进行指标权重的确定,通过两次一致性检验去掉不合理的数据,使得结果接近实际。
3结果与分析
本次采用Matlab程序的[V,D]=eig(A)格式计算矩阵的特征值和特征向量。
3.1 A-Bi权重值计算与分析通过Matlab计算可以得到A-Bi的判断矩阵的计算结果,如下表1所示。
由表1可知权重值为:技术指标 > 经济指标 > 环境指标。其中技术指标占到49.3%,说明在烟气脱硫的工艺选择中,二氧化硫达标排放是非常重要的。
3.2 Bi-Ci权重值计算与分析
对矩阵Bi-Ci进行计算,矩阵Bi-Ci的排序权重值如下表2。
由表2分析可知:
①B1的层次单排序中,子指标排序C2>C1,说明C2(脱硫成本)比C1(单位投资)重要。
②技术指标B2中,C3和C6的值较大,因此脱硫率和技术成熟度的权重比较大。
③在环境指标(B3)中,副产物的回收性(C11)相对重要。
3.3 Ci-Di权重值计算与分析
对矩阵Ci-Di进行计算,矩阵Ci-Di的排序权重值如下表3。
在11个次级指标中,脱硫率(C3)的比重很大,从上表3中可以看出,D1和D3的综合性能较好,D1和D3权重值的直观图如下图2所示。
由上图2可知,11个参选因素中,烟气循环流化床脱硫工艺有C1、C2、C4、C7、C9、C10等六个参数的排序权重值比石灰石/石膏湿法脱硫工艺大。
3.4 C、D层次排序权重值计算与分析通过计算,D层次5个脱硫工艺的权重排序值的直观图如下图3:
上图3中各工艺的层次总排序结果表明:D3(0.274) > D1(0.231) > D5(0.194)> D2(0.157)>D4(0.144),可知5个工艺中,烟气循环流化床工艺的重要性最强,其次是石灰石/石膏湿法脱硫工艺,然后依次是电子束法、旋转喷雾干燥法,最后是炉内喷钙脱硫尾部增湿脱硫工艺。
因此由层次分析法判断得出,烟气循环流化床脱硫工艺的综合性能最好。
4结语
其一,建议A电厂选择循环流化床锅炉炉内固硫+烟气循环流化床脱硫工艺的组合工艺进行脱硫,不应该盲目选择脱硫效率很高的石灰石/石膏湿法脱硫工艺。
其二,针对含硫率在3.92%以下的高硫煤炭,CFB锅炉炉内固硫+CFB-FGD的两级脱硫工艺能使电厂烟气稳定达标排放,本文提出的两级脱硫的组合工艺可以在重庆地区推广。
参考文献:
[1]郝吉明.燃煤二氧化硫污染控制技术手册.北京:化学工业出版社,2001.
[2]国家经贸委.火电厂烟气脱硫关键技术与设备国产化规划要点[R].北京:2007.
脱硫工艺论文篇5
随着2014年对标工作和降本增效工作的实施和考核,作为一名技术员深感约成本的重要意义,虽然创效困难程度很大,但是如何能够大幅度的降低成本,除了管理到位,我坚信依靠改变工艺和原材料将是最佳途径,作为一名老烧结技术员,当看到除尘灰在运输生产过程中、下料堵仓过程中产生的诸多不利因素和造成现场环境的二次污染以及给岗位工造成的巨大劳动强度后,我想到了型煤工艺,结合其他厂家的先进设备,我想将除尘灰、烧结矿返矿再粉碎后再惨加一些如焦沫、无烟煤等物质后,让其在一定的型煤设备上高压下就能造出直径30-40毫米左右的球状体,大家知道除尘灰、返矿在一定程度上是烧熟了的小粒度烧结矿,若将其做为铺底料,对生成的烧结矿成品质量影响不大,但是产量肯定是增加的,所以想采用除尘灰、返矿做铺底料工艺;另一方面,自从2013年我们龙钢烧结厂有了脱硫工艺后,每日就能产出200-300吨的脱硫石膏,而这些脱硫石膏被当作垃圾处理给环保公司,每车还需付装运费150元。根据自己多年的经验,我知道石膏的成分主要是二水硫酸钙,而二水硫酸钙在1400℃下加热就会产生出氧化钙和二氧化硫,在烧结工艺条件下,大约1250℃石膏就会分解成氧化钙和二氧化硫,大家知道:二氧化硫有95%被燃烧释放变成三氧化硫,随烟气排出,剩下的氧化钙就是我们理想的熔剂生石灰的主要成分。
一个大胆的设想用石膏替代生石灰的工艺就在我的脑子里成型,经过自己多次的私下制作的简易实验装备,用我们现用的混匀矿,加入一定的石膏配比,再经过制粒混匀,终于在台车上烧制出了碱度为1.97的54.5%的全铁品位烧结矿。虽然粒度组成中大于16毫米以上的比例较少仅占56-42%,转鼓强度仅达到58-75%,今后还需要继续探求更高烧结矿工艺技术指标。
1 理论、实践依据
大家知道:压球机主要用于有色和黑色金属矿粉的制球造块,使其直接进炉冶炼,提高附加值。凡是冶金行业废料,辅料需上炉的,都需要用压球机来完成。例如:郑州威力特机械设备有限公司研发生产的型煤压球机、干粉压球机、脱硫石膏压球机等压球机系列产品技术先进、质量可靠、一机多用。同时具有成型压力大、主机转数可调、结构紧凑、便于维修、配有螺旋送料装置特点。适合大、中、小型企业建立具有一定生产规模的生产线。
成功案例:冶金企业把粉状物料压成球团,回炉冶炼,扩大了物料的使用范围;耐火材料企业把粉料压成球团,煅烧后提高了物料的纯度;化肥企业利用粉煤压成球团制造气型煤,达到降耗增收;这些都是各类企业利用球团技术的范例。样品球如图1。
结论:综上所述,可见将除尘灰、返矿压制成20-40mm球状体是可行的。
2 将脱硫石膏烧制成生石灰的理论研究
2.1 脱硫石膏介绍
脱硫石膏是烟气脱硫中石灰石粉末与二氧化硫反应产生的工业副产物,主要成分是二水硫酸钙,其特点是:纯度高、成分稳定、粒度小、粉状、游离水约12-17%,颗粒大小、粒径分布均匀,级配较差,标稠用水量大,含有一定量的碳酸钙和较多的水溶性盐,根据燃烧的煤种和烟气除尘效果的不同,脱硫石膏从外观上呈现不同的颜色,一般我们视角看到的都是灰黄色或灰白色,质量优良的脱硫石膏是纯白颜色。但实际呈现的是灰色、黄色、灰褐色、红褐色等。
粉状脱硫石膏在运输和生产中有诸多不便,由于其含水分比较大,运输成本高,其次也是最主要问题,湿基脱硫石膏粘结性强,直接生产线上应用很容易粘堵输送装置、料斗、球磨机,无法正常生产。若能把湿基脱硫石膏成球、烘干就可以解决以上问题。
2.2 将脱硫石膏制成球状体不成问题
2.2.1 脱硫石膏压球机简介
根据石膏性能,巩义市曙光机械厂已开发出新型高效节能压球机,产量在5~30吨/时,脱硫石膏压球机能将脱硫石膏粉末一次性压制成球,产量大、成球率高。该设备能将脱硫石膏粉末,在不需要添加任何粘合剂情况下一次性压制成球,且成球率在95%以上,压出来的球硬度很强,搬运装卸不宜破碎。
2.2.2 脱硫石膏压球机工作原理
脱硫石膏压球机成型机的主要机型是对辊成型机(人们常说的压球机),它有一对轴线相互平行、直径相同、彼此间有一定间隙的圆柱形型轮,型轮上有许多形状和大小相同、排列规则的半球窝,型轮是成型机主部件。在电动机的驱动下,两个型轮以相同速度、相反方向转动,当物料落人两型轮之间在结合处开始受压,此时原料在相应两球窝之间产生体积压缩;型轮连续转动,球窝逐渐闭合,成型压力逐渐增大当转动到两个球窝距离最小时成型压力达到最大。然后型轮转动使球窝逐渐分离,成型压力随着迅速减小。当成型压力减至零之前,压制成的脱硫石膏就开始膨胀脱离。
2.2.3 脱硫石膏在生产上的应用可能性
龙钢有155m3石灰竖窑5座,如果将脱硫石膏当做30-40mm的石灰石放在
155m3石灰竖窑上进行煅烧(窑体设计上需要增加一套烟气脱硫设施、温度需要提高到石膏分解温度范围内),这样一来,用石膏完全可以生产出替代品石膏灰,成分含量理论上应差别不大。考虑到脱硫石膏负成本,那么用石膏灰替代生石灰(300元/吨),其理论效益相当可观。
3 从专家、教授发表的学术论文看石膏加热分解成生石灰氧化钙也是可行的
3.1 上海华东理工大学著名教授高玲、唐黎华等教授联名发表过论文《不同气氛下硫酸钙高温分解热力学分析》,在此文中明显指出在氧化气氛下,温度达到1700℃,硫酸钙很难分解,但在石墨弱还原气氛下、氢气气氛下硫酸钙的起始温度均低于1000℃。特别是在氢气气氛下,硫酸钙完全分解的最高温度不超过1300℃,再加压条件下44分钟后就可100%转化分解。
3.2 教授卢平、章静在论文《脱硫石膏还原分解特性的实验研究》中提出了850-1050℃硫酸钙分解的可行性。
3.3 教授韩翔宇、陈浩侃、李保庆联名在论文《硫酸钙氢气气氛下的热重研究》中指出在氢气气氛下、加压条件下1000℃以前,硫酸钙分解出的产物主要是硫化钙,1000℃以后,硫酸钙和硫化钙之间发生固相反应会生成氧化钙。
4 作者的实验过程
总结以上所述,在理论上和实践上,前辈们都给我们指明了方向,经过多次努力,做了实验如下:
4.1 将石膏用一定的简易设备加压将其压制成型为20-40毫米的石膏半球-球体(此设备及工艺已经成熟应用在河南、山东等地);
4.2 将其放在实验室的马弗炉中进行烧灰实验,经过多次的温度控制和加入一定的催化剂气体,最终在适当的温度下终于烧成了氧化钙含量为40%的熟石灰(其成分和生石灰的基本一样)。
4.3 用现场的含铁混匀矿垛料,加上多次设置的配比制成烧结混合样,在经过人工混匀制粒后,将其200kg放到400m2台车上布料、调温,经过多次操作终于在台车上烧制出了碱度为1.97的全铁品位为54.5%的烧结矿(其他成分基本符合要求,除过硫含量3.0%)。这样从理论到实践上证明了所想的工艺的可行性。兴奋之余,作者将想法告诉现任的上级技术领导:科长、调度长、技术厂长,希望得到他们的支持和进行下一步较大规模的实践,却被他们以不成熟搁浅了,实践到此为止。
4.4 思考
4.4.1 实验做出的含硫3.0%的烧结矿成品样,对炼铁生产来讲是不符合生产需要的,在实验条件下,其烧结矿中的硫还未能完全分解掉,在化验室中烧成的氧化钙只有40%这一点可以证明还未烧透,或者还只是半成品硫化钙,只有当氧化钙含量化验数据在80%左右时才算试验成功。故还需要做进一步的实验研究;
4.4.2 当采用石膏大量替代生石灰后,龙钢烧结烟气脱硫系统中的二氧化硫含量将不再是1500-2000mg/m3,有可能增加到3000-5000mg/m3,这将会增加脱硫设备的负货。
5 结束语
(1)用除尘灰、返矿制作成20-40mm的铺底料这一工艺,本身就是一大胆创新,完善它并将其应用于烧结工艺中很有现实意义:增加产量、变粉为块,增强烧 结透气性、降低成本,这一点领导是认同的,但需要增加新设备投资,然而在可行性操作实验上,分厂领导不支持,使得计划只得停留。
(2)用石膏部分代替或全部代替生石灰工艺更是一次革命:因为石膏没成本、粒度满足混合料要求、且水分适中。而生石灰的市场价在300元以上。按每月消耗现在665m2烧结机产能需要生石灰84000吨计算,年节约在3亿余元以上;从环保角度讲,变废为宝,还能减少生石灰的制造、拉运方面的人、财、物的投资消耗,其社会效益将会更加巨大;石膏替代生石灰在烧结工艺中还可减少给配料环境造成的污染。由于我厂还未能将石膏沫状变成球状体、在石灰窑上烧制出石膏灰的现实,加上我厂领导还担心混合料的温度有所下降以及用此新工艺不成熟有风险。虽然我坚持解释到:生石灰理论上能提高料温10-15℃,实际上能提高10℃左右 ,就按10℃的热量我们完全可以用增加焦沫配比1-2%来彻底解决料温问题,再综合计算成本,烧结矿的成本还可再降50元以上,其效益也是相当可观的;
(3)考虑到此工艺若能够被推广或普及到全社会,这将是一次工业化革命,其意义将不可估量。非常期待看到或得到全社会各行专家教授关于此工艺方面的更工业化的实验研究结果,更希望同行们对分析研究给予批评指正和提出宝贵意见。
参考文献
脱硫工艺论文篇6
焦炉气制甲醇具有成本优势,目前,伴随着对焦炉气制甲醇的认识度越来越高,利用焦炉气生产甲醇的企业也越来越多。但是焦炉气中硫化物成本比较复杂,容易造成设备腐蚀,对环境也造成污染,而且焦炉气制甲醇装置中,容易造成下游甲醇合成催化剂中毒失活。
焦炉气中甲烷的转化有催化转化和非催化转化两种方法,目前,国内多采用催化转化方法,焦炉气中家硫化物的脱除使用的是高温加氢脱硫工艺,将有机硫转化为容易脱除的H2S再进行脱除,然后送入转化炉。而采用非催化转化方法的装置中,转化后的合成气自湿法脱硫和脱碳后,经压缩气体温度达到90~150℃,如果采用高温精脱硫路线,需要将气体温度提到350~400℃。能耗较高,如果采用常温精脱硫路线,又需要将气体温度冷却至常温来操作,然后提温进入甲醇合成塔。不管是高温路线还是常温路线,都会造成精脱硫工艺流程复杂,带来能源的附加消耗,因此开发适合于该工况的中温精脱硫新工艺具有十分重要的意义。
一、中温精脱硫新工艺及精脱硫剂的介绍
(一)中温精脱硫新工艺的简介
中温精脱硫新工艺由DJ-1多功能净化剂串EZ-3精脱硫剂组成,DJ-1多功能净化剂的作用是将焦炉气中的COS转化为H2S,EZ-3精脱硫剂作用是将H2S脱除。该工艺具有以下特点。
1.净化度高。
2.DJ-1多功能净化剂可以抗微量氨干扰。微量氨短时冲击后,可以恢复活性,脱硫效率不受影响。
3.该工艺使用温度范围宽,90~220℃工况下都能达到净化指标要求。
3.使用空速大。
精脱硫剂简介
1.精脱硫剂物理指标。见表一
表一 脱硫剂物理指标
2.反应原理
(1)DJ-1多功能净化剂
二、中温精脱硫新工艺在焦炉气非催化转化制甲醇装置中的应用
(一)工艺参数
1.焦炉气制合成气气体组分
2.中温精脱硫段工艺指标
(二)工艺流程
工艺流程,如图一
三、中温精脱硫新工艺在焦炉气非催化转化制甲醇装置中的应用
中温精脱硫新工艺脱硫精度高,反应速度快,工作硫容大,强度和耐水轻度好,使用化工原料的精脱除,在具体的焦炉气非催化转化制甲醇装置中应用稳定,在实践中取得了很好的成效,相比其它的精脱硫工艺有比较明显的优势,目前已经被广泛的推广和应用。中温精脱硫新工艺在焦炉气非催化转化制甲醇装置中的应用,自系统研制运行以来,取得了很好的成绩,精脱硫系统开车以来,运行平稳,脱硫效果好,能够有效的满足企业需求,据精脱硫系统运行的相关数据表明,中温精脱硫新工艺净化度高,出口总硫≤0.1×10^6,保证了甲醇装置长周期的稳产高产。如表二
三、结语
该工艺是在传统高温及常温精脱硫工艺路线的基础上,实现中温精脱硫新工艺。中温精脱硫新工艺净化程度高,出口总硫≤0.1×10^6,经多年实践运行经验表明其无流醇、硫醚等生成的副反应,完全满足市场对精脱硫的基本要求,同时它又改变了以往硫含量过高的问题,保护了甲醇合成催化剂,为企业稳定、增长起到了重要的作用,为其它合成气精脱硫中的应用提供了借鉴依据。
参考文献
[1]巨涛.甲醇合成系统精脱硫技术改造总结[J].化工设计通讯.2012.
[2]李树长;;焦炉气精脱硫指标及保证措施[J];河北化工;2010年03期
[3]刘敬尧;何畅;李;李秀喜;钱宇;;以合成气为核心的多联供多联产集成能源化工系统[J];煤炭学报;2010年02期
[4]王清涛;丁心悦;杨大庆;刘文芳;张洪涛;;焦炉煤气无水氨脱氨净化技术的国产化[J];煤化工;2010年05期
脱硫工艺论文篇7
随着胜利油田油气藏开发进程的逐步深入,稠油热采规模的不断扩大,部分采油厂热采井出现不同程度的硫化氢含量上升趋势,含硫化氢油井逐渐增多,浓度逐渐升高。以孤岛采油厂为例,目前已有16口井天然气中硫化氢含量达到150ppm以上,由于原油中含硫化氢使的溶液呈酸性,加速了腐蚀,另外硫化氢腐蚀可造成碳钢管线的氢脆、断裂和穿孔,给生产带来很大安全隐患,硫化氢气体扩散对周围环境造成较大影响,拉油罐车在运输过程中有硫化氢气体逸出对沿线的人员造成安全隐患。因此开展井口原油和天然气中硫化氢脱除工艺技术的研究势在必行。
2 稠油热采井口采出液特点分析
稠油采出液中硫化氢分布在原油、水、气中,由于硫元素种类和分布形态的多样化的影响,给采出液中硫化氢的测试带来较大困难。通过查看现场生产数据,发现单井中的伴生气较少,原油含水较多,气油比大约在1:17.5左右,含水量在90%以上,采出温度在40~60℃之间,采出压力在0.5~0.6MPa之间。通过取样检测油样发现,使用热采的井口的稠油粘度很高,一般在5Pas以上,流动性差。
单井稠油粘度大、气液比小等特点,使原油中的硫化氢向气相中转移释放困难,且现场空间资源有限,无法进行掺稀降黏,增加了硫化氢脱附难度。
所以对脱硫工艺提出了,脱硫工艺简单、装备紧凑撬装、体积小,可以进行整体运输。
3 井口一体化脱硫工艺
原油井口生产设施少,单井相对独立,气液比低,且不具备掺稀降黏因此井口原油脱硫装置要求装置简单,占地面积少,配套设施少。基于以上要求提出采用原油气提脱硫+天然气脱硫净化的一体化脱硫工艺。
含硫单井来液通过粗分水后,原油加热,从气提脱硫塔第一块塔板进入,依次经过塔内各层塔板,与从气提脱硫塔底部进入的净化天然气逆流接触,原油中的硫化氢通过扩散作用进入到天然气中;分离出来的水从气提脱硫塔下部进入,依次经过塔内底部塔板,与从气提脱硫塔底部进入的净化天然气逆流接触,水中的硫化氢通过扩散作用进入到天然气中;含硫天然气从塔顶进入天然气脱硫塔,在塔内经过脱硫剂处理将硫化氢脱除,净化天然气从塔顶出来后经过增压风机增压后进入气提脱硫塔,气提含硫原油,重复循环,剩余的净化天然气与脱硫后的原油在混合器内混合后外输。
4 工艺模拟
工艺流程中脱硫过程分为原油气提脱除硫化氢和天然气中硫化氢的脱除,其中原油气提脱除硫化氢受到气提气量、气提压力、塔器内部结构、原油温度等关键因素的影响,而天然气脱硫净化处理目前工艺技术相对成熟,有诸多的工程实践经验,对于小气量、低含硫的单井天然气,其潜硫量相对较低,采用氧化铁、氧化锌等干法脱硫工艺具有设备少,流程简单,配套少,操作方便等优点,适合井口脱硫处理。
针对原油气提脱硫工艺采用PRO II软件进行了气提气量、压力、塔板数、原油温度的模拟研究,探索其相互影响规律。通过选取孤岛某口井采出液的物性作为模拟的输入边界条件。
4.1 基础参数
温度:50℃ 压力:0.6MPa
原油量:4t/d 水量:55t/d
原油性质:通过实沸点蒸馏曲线、粘温曲线得到
天然气含硫化氢量:4000ppm
原油组成:
天然气组分:
目标:原油中硫化氢含硫小于60mg/kg
4.2 模拟结果分析
从图中可以看出随着原油温度的增加,脱硫效果变化明显。考虑到采出液中水含量较多且水的热熔大,所以采取油水分开加热分别进塔。通过实验表明水中含硫化氢很容易气提,所以原油从气提塔上部塔板进入,水从气提塔下部塔板进入,在保证原油温度、粘度和不影响气提脱硫效果的同时较少能耗。
从图中可以看出,随着气提塔塔压的升高,原油脱除硫化氢效果变差。随着压力的升高,天然气中硫化氢的分压相应升高,不利于硫化氢向天然气中扩散,从而造成原油中硫化氢含量升高,因此,在实际流程设计时,在能够满足原油外输和天然气净化处理的条件时,尽量降低气提压力,利于原油脱硫效果。
5 结论
为解决原油天然气中由于含有硫化氢对生产和人员而造成的影响,以原油和天然气脱硫为解决途径,结合井口生产的特点和输送工艺的不同,提出了井口原油天然气一体化脱硫工艺,并针对原油气提脱硫进行了工艺模拟,研究了气提气量、压力、温度等因素对气提脱硫效果的影响规律和关系。
本文模拟计算为气液完全平衡,但在实际生产运行中原油黏度,含水等因素会对气提脱硫效果产生一定影响,在高含水情况下存在水包油型乳化现象, 低含水状态下存在油包水型乳化现象, 这些都会造成在脱硫塔内无法达到完全的气液平衡, 降低脱硫效果[4],因此应当进一步开展这方面的相关理论与实验研究,为工程设计提供可靠地数据参考。
参考文献:
[1]冯叔初等.油气技术与矿厂加工[Z].
[2]孔伟等.塔中油田汽提法原油脱硫化氢工艺技术.天然气与石油,2012(06):34-35.
脱硫工艺论文篇8
近些年来,酸雨产生的危害是有发生,导致了大量鱼类死亡、湖泊退化等现象,导致酸雨的原因方面很多,而普遍都认可的便是二氧化硫是酸雨的主要成分之一,而发电厂又常常被认为二氧化硫的主要排放源之一[1,2]。
因此,提高发电厂环保措施,特别是烟气脱硫工艺的提高,可以减少二氧化硫的排放量,进而控制酸雨的形成起到了重要作用。目前,在电厂烟气脱硫中主要有干法脱硫和湿法脱硫两类[3,4]。而湿法脱硫技术是采用液体的吸收剂进行脱硫,由于气液传质比干法的气固传质要更快,所以湿法在烟气脱硫中交往受欢迎。而在湿法脱硫中,双碱法脱硫工艺师当前较为广泛采用的工艺之一,钠钙双碱法是较为常用的脱硫方法之一,该法由于具有吸收效率高等特点在国外广为应用,像日本和美国目前已有50套以上的钠钙双碱法应用于电厂烟气的脱硫。本文结合电厂的基本情况详见论述了钠钙双碱法在烟气脱硫中的应用及相应的问题,本文的研究对电厂烟气脱硫有一定的总结意义。
二、双碱脱硫工艺
通常,在电厂烟气双碱脱硫工艺是相对于石灰/石灰石法来说的,石灰/石灰石法虽然脱硫率较高,但是存在着石灰石溶解问题易导致结垢堵塞吸收系统的管道等问题,而双碱法采用两种不同的脱硫剂即氢氧化钠(或碳酸钠)和石灰,该方法成功解决了结垢堵塞问题。
1.双碱脱硫工艺的基本原理
双碱脱硫工艺具体过程包括吸收脱硫和再生两步。为氢氧化钠(或碳酸钠)溶液为启动脱硫剂,该溶液作为循环脱硫液进入电厂的脱硫系统进行脱硫。吸收烟气的二氧化硫之后循环液进入沉淀池,通过沉淀等去除烟尘之后进入反应池,在反应池中投加石灰进行反应,置换出即氢氧化钠(或碳酸钠),再次进入循环脱硫系统。
2.双碱脱硫工艺的优点
双碱法脱硫技术作为一种湿法脱硫工艺与其他脱硫工艺具有非常明显的优势,表1列出了与部分脱硫工艺的对比。
从表1中可以归纳出双碱法脱硫的主要优点如下:
2.1吸收效率高。钠基吸收剂相对于钙基吸收剂直接吸收二氧化硫相比,钠基吸收剂吸收二氧化硫属于气膜控制,即液相吸收速度快,大大提高了吸收效率。
2.2产物溶解度大解决了结垢等问题。双碱脱硫工艺是在石灰法基础上的改进,由于生成的钠盐相对于钙盐更易容易水,解决了石灰脱硫技术这种钙基吸收生成溶解度小的钙盐导致管道或者脱硫塔的结垢进而导致堵塞的缺点。
2.3能耗较低。由于吸收剂的再生在脱硫塔之外的反应池进行,可以避免了脱硫塔的磨损和堵塞,可以提高运行稳定性,进而降低运行成本。
2.4无二次污染现象。
三、双碱脱硫工艺在国内的应用现状及主要问题
1.国内电厂烟气脱硫的应用现状
进入新世纪以来,二氧化硫的排放量逐年增多,而作为二氧化硫主要的贡献源的火力发电厂随着装机容量的增多,例如2005年我国火电装机容量达到5.08亿千瓦,这比2002年装机容量多出1倍多,二氧化硫的排放量增加了27.8%[5]。快速发展是导致SO2排放量增加的主要原因二氧化硫的排放也不断也不断增多,例如1998年火力发电厂的二氧化硫排放量占到全国总排放量的将近四成,但是到了2010年就达到了六成之多。
目前,为了减少二氧化硫的排放,各种脱硫工艺得到不断的发展,其中湿法脱硫占到了85%以上,在湿法脱硫中钠钙双碱法目前也成为较为普遍采用的脱硫工艺。在我国,双碱脱硫工艺工业化应用的单机规模最大的达到了100MW,成功的实例也很多。双碱脱硫技术是仅次于石灰石/石灰-石膏脱硫技术的湿法脱硫方法。
2.双碱法脱硫出现的问题
2.1烟气中亚硫酸盐去除不高导致烟囱腐蚀严重[6]
双碱法去除烟气中的二氧化硫的效率很高,但是对于其他含硫物质的去除效果并不明显,例如SO32-,而较低的去除率导致烟气中亚硫酸盐较多,在湿度较大的烟气中对烟囱和管道都会产生严重的腐蚀现象。近些年,在一些发电厂该种烟囱由于亚硫酸盐的腐蚀而出现问题的事情非常多。
2.2钠基脱硫剂消耗量大,成本高
目前,困扰双碱脱硫技术的主要问题是再生反应阶段,即亚硫酸钠置换形成新鲜吸收剂氢氧化钠的过程效率不高。这将直接导致大量的钠盐进入废水或者其他途径而消耗掉。这势必导致补充大量的新鲜钠基脱硫剂,这就增加了脱硫剂费用和运行成本。
2.3含硫废水和脱硫灰渣对环境产生危害
双碱法脱硫产生的脱硫废水和脱硫灰渣处理不当容易对环境产生危害。如脱硫废水在外环境中被硫酸盐还原菌还原成硫化物,会影响周围环境水体的水质。脱硫灰渣处理不当容易引起空气扬尘。
四、有关问题的解决方法
1.针对腐蚀问题,应优化工艺和提高烟气输送管道和烟囱的设计
主要包括:工艺上提高除雾器的去除效果,减少烟气湿度;提高烟囱和管道的防腐质量;采用效果更好的防腐材料。
2.改进双碱脱硫工艺提高石灰置换成亚硫酸盐的效率
例如,采用更搞笑的置换反应器以提高置换率,减少钠基脱硫剂的补充量;工艺上优化操作参数,如反应器的搅拌速度的优化提高传质。
3.采用更加有效的环保措施
针对含硫废水提出回用处理措施,提高回用率甚至提出废水的零排放;针对灰渣要做到及时清理,将灰渣综合利用等。
五、展望
目前,在发电厂烟气脱硫工艺中,由于各种原因仍然以石灰石/石灰-石膏脱硫为主,然后双碱法脱硫工艺由于具有更大的优势,其必将在脱硫工艺中占到更大的比例。在当前环保意识提高和环保政策严格的情况下,应该建立健全烟气脱硫的法律、法规和执法力度,并提高企业的环保意识,并合理的利用烟气脱硫工艺,特别是从众多的烟气脱硫工艺中选出更加合理的方法,并在实际运行过程中不断优化,更好的减少二氧化硫的排放,以便减少酸雨对环境的危害。
参考文献
[1]国家环境保护总局.国家酸雨和二氧化硫污染防治“十一五”规划[EB/OL]. (2008-01-17)http:// sepa. gov. cn/info/gw/huangfa/200801 /P020080117479516237831
[2]国家环境保护总局.国家环境保护“十一五”规划[EB/OL].[2008-01 -18] http: // sepa. gov. cn/plan/hjgh/sywgh/gjsywgh/200801 /t20080118_116458. htm
[3]周玉新,刘建章.烟气脱硫技术现状与发展趋势[J].化学工程师, 2007, (10): 38.
[4]董佩杰.火电厂烟气脱硫技术的探讨[ J].山西电力, 2006,(4): 63~65.
脱硫工艺论文篇9
1迁移规律
1.1 煤中硫的存在形态
煤中的硫主要以无机硫和有机硫两种形态存在,无机硫的主要形态是硫化物(大部分以黄铁矿FeS2 硫形态存在) 、硫酸盐(主要为硫酸钙和硫酸铁等) 和元素硫(微量) ; 无机硫中以硫铁矿形式存在的硫占绝大部分, 并以大块团聚或是非常精细的小颗粒(直径0.1~0.6μm) 镶嵌在煤的大分子结构里; 以硫酸盐形态存在的硫数量很少超过煤总量的0.1 % , 在一些风化煤里还可能发现少量的元素硫, 它是黄铁矿氧化后的产物,一般在新开采的原煤里很少发现。
煤中的有机硫绝大多数属于煤质大分子结构的一部分, 以桥键形式连接煤质大分子的各个环, 与煤的大分子网络结构交联在一起。煤中的有机硫约占总硫的1/3~1/2 左右, 按其结构可以分为脂肪族硫、芳香族和杂环族硫三类, 包括硫醚(脂肪族或芳基) 、硫醇(脂肪族或芳基) 、噻吩、环硫醚等。最主要的几种有机硫为二苯并噻吩、噻吩、脂肪族硫醚等。含硫官能团的反应性与和硫原子相连的取代基结构有关。硫醇、硫醚比较活泼, 在成煤过程中, 硫醇依次向硫醚、噻吩结构转化。
1.2 煤热解过程中硫的迁移
煤在焦炉中的热解温度约为1000~1100 ℃, 煤中的无机硫中的硫酸盐的分解温度约为1350 ℃, 所以硫酸盐硫基本上不分解而进入了焦碳中, 而硫化铁硫、元素硫和各类有机硫在800 ℃时可完全分解, 所以硫化铁硫及各类有机含硫化合物逐渐分解, 一部分以气体形式释放, 少量冷凝在焦油中, 热解过程中释放的H2S气体大部分来源于硫铁矿和脂肪族硫的分解, 程序升温热解试验表明, 400 ℃以下H2S 的释放来源于脂肪族硫化物的热分解, 400~700 ℃范围内H2S 的释放则对应于芳香族硫的分解, 部分H2S 由于传质限制在高温下进一步与煤中有机质发生反映生成更稳定的有机硫,从而进入焦碳的碳硫复合体, 如噻吩存在于煤焦中,发性硫成分复杂, 达数十种之多, 其中H2S 和焦油硫在所有产物中所占比例最大, 是重要的挥发性硫。
炼焦用煤就全国平均来说有机硫与硫铁矿硫的比例约为4∶6 , 硫酸盐硫所占比例甚微(不同地区所产精煤比例会有不同, 本文仅就平均而言) , 根据以上硫元素迁移转化规律, 我们总结为:
煤中的硫份在热解过程中约60 %~70 %最终固定于焦碳中, 由焦碳带出, 约小于1 %固定于焦油中, 由焦油带出, 其余部分转入煤气中, 其形式复杂, 但绝大多数是以H2 S的形式存在, H2 S硫约占煤气含硫的90 %以上。焦炉荒煤气经脱硫后绝大多数硫元素以单体硫的形式脱出, 煤气再经硫胺及脱苯等工序, 剩余的少数硫由粗苯等产品部分带出; 净化后的净煤气部分回炉燃烧, 其内的H2S 最终被氧化以SO2 形式排放,剩余净煤气可用于锅炉、粗苯管式炉、发电或作为化工原料使用, 如果用于发电或锅炉等燃烧工艺, 则最终硫元素以SO2 形式排放。
荒煤气在冷鼓及蒸氨工序极少数硫元素被氨水吸收以硫化物形式进入蒸氨废水, 从而进入水体; 由于焦炉为正压, 由炉顶、炉门等处泄漏的炉气中的H2S在高温的作用下, 遇氧气大部分被氧化为SO2 并无组织排放; 热装热出焦炉在装煤和出焦过程中, 在高温的作用下, 炉气中的H2S 也大部分被氧化为SO2 , 并无组织排放。
2 硫的去向
物料平衡是工程分析常用的计算方法之一, 其特点是污染物分析全面, 计算结果准确性高, 但所需的资料多, 过程复杂, 难度较大, 且需要对生产工艺有较深刻的了解。硫平衡就是根据该计算方法分析得出的, 它是在对工艺全过程生产及管理全过程有深入的了解并进行充分分析的前提下, 根据物质守恒定律,对生产过程的物料( 原料和燃料) 、投入和产品产出(包括主要产品、副产品和其他伴生物质等) 的平衡关系来确定各个工艺过程硫的去向。
焦化生产工艺流程简述。焦化工程生产工艺为外购原煤经过洗选, 洗出精煤、中煤、矸石和煤泥, 中煤和煤泥外售, 洗精煤配合、粉碎后, 送入焦炉炭化室内高温干馏炼焦制气,焦炭筛分后外售。炼焦过程中产生的荒煤气经冷凝、鼓风、电捕焦油、脱硫及硫回收、硫铵、洗脱苯后,作为焦炉、发电、锅炉等使用, 或外供其他工业用户使用, 在煤气净化过程中回收的焦油、粗苯、硫磺、硫铵外售。
3 焦化生产工艺中硫污染减排分析
焦化企业硫污染减排途径主要有以下几种:
(1) 原料煤的选择。焦化项目排入大气中的二氧化硫全部来源于原煤中的含硫, 无论是降低煤中的有机硫或无机硫, 首先要降低煤中的全硫含量。要实现这一目标, 首要的是要选用低硫煤, 其次通过原煤洗选可将煤中灰份降低, 从而降低煤中无机硫的含量, 通过以上措施可将洗精煤含硫量控制在0. 5 %左右, 从而有效实现二氧化硫大幅度减排。
(2) 高烟囱排放。目前企业中采用较多的方法是高烟囱排放, 增加出口处烟气排放速率, 利用大气稀释扩散能力, 降低SO2 落地浓度, 减少其对地面上人和动植物等的危害。该法存在扩大污染面、形成酸雨区、对控制排放总量没有贡献等弊病。同时烟道的造价与高度平方成正比, 所以此法只能作为一种辅助和过度的方式, 或在局部区域内使用有效。
(3) 采用清洁生产工艺及先进生产设备。焦炉生产过程中炉体的无组织排放如炉门、炉顶、装煤、出焦会产生大量的无组织污染物排放, 要彻底解决这一问题首先要采用大型全自动化、全程控机械化焦炉, 大型焦炉都有专项设计以解决这些问题, 同时应配套干熄焦系统以减少污染物的排放。其次, 针对装煤、出焦要同步配套高捕集率除尘脱硫地面站, 变无组织排放为有组织排放, 从而有效实现二氧化硫的减排。
(4) 荒煤气脱硫技术。煤中约三分之一的硫以气态形式进入荒煤气中,因此荒煤气脱硫就成为二氧化硫减排的关键措施。焦炉煤气脱硫工艺有干法、湿法脱硫两大类。干法脱硫多用于精脱硫, 对无机硫和有机硫都有较高的净化度。不同的干法脱硫剂, 在不同的温区工作, 由此可划分低温(常温和低于100 ℃) ; 中温( 100 ~ 400 ℃) ; 高温( >400 ℃) 脱硫剂。
干法脱硫由于脱硫催化剂硫容小, 设备庞大, 一般用于小规模的煤气厂脱硫或用于湿法脱硫后的精脱硫,对低浓度H2S 具有较好脱硫效果, 脱硫效率可达到99 %。
当煤气量大于3000Nm3/h时主要采用湿法脱硫。焦炉煤气湿法脱硫方法的选择首先是碱源的选择, 碱源有氨、纯碱、有机溶剂醇类如二乙醇胺等。
目前我国已经建成( 包括引进) 的焦化工程采用的具有代表性的湿法脱硫工艺有以下几种:
湿式氧化工艺:
TH 法以氨为碱源
FRC 法以氨为碱源
ADA 法以钠为碱源
HPF 法以氨为碱源
湿式吸收工艺:
索尔菲班法;单乙醇胺法AS 法;氨硫联合洗涤法。
总之, 荒煤气脱硫无论干法或湿法工艺, 都已广泛应用于我国焦化领域中, 技术成熟可靠。对于焦化企业来说, 关键是要根据企业的实际情况, 针对性地同步配套煤气脱硫设施, 杜绝荒煤气直排。
脱硫工艺论文篇10
1、湿法烟气脱硫
1.1工艺原理
烟气进入脱硫装置的湿式吸收塔,与自上而下喷淋的碱性石灰石浆液雾滴逆流接触,其中的酸性氧化物SO2以及其他污染物HCL、HF等被吸收,烟气得以充分净化;吸收SO2后的浆液反应生成CaSO3,通过就地强制氧化、结晶生成CaSO4·2H2O,经脱水后得到脱硫副产品—石膏。
1.2主要反应过程
SO2+H2O=H2SO3 SO3+H2O=H2SO4
CaCO3+H2SO3=CaSO3+CO2+H2O
CaCO3+H2SO4=CaSO4+CO2+H2O
2CaSO3+O2+2H2O=2CaSO4·2H2O
1.3工艺特点
脱硫效率高、设备小、易控制、占地面积小以及适用于高中低硫煤等;除在燃煤发电厂获得广泛应用外,在硫酸工业、钢铁工业、有色冶金工业、石油化工以及燃煤工业窑炉等烟气脱硫中也获得广泛的应用;技术进步快。
2、喷雾干燥法脱硫
2.1工艺原理
以石灰为脱硫吸收剂,石灰经消化并加水制成消石灰乳,消石灰乳由泵打入位于吸收塔内的雾化装置,SO2被雾化了的Ca(OH)2浆液或Na2CO3溶液吸收;温度较高的烟气干燥了液滴,形成干固体废物,由袋式除尘器或电除尘器捕集。脱硫后的烟气经除尘器除尘后排放。
2.2主要反应过程
SO2+Ca(OH)2=CaSO3+H2O SO3+Ca(OH)2=CaSO4+H2O
SO2+Na2CO3=NaSO3+CO2 SO3+Na2CO3=NaSO4+CO2
2.3工艺特点
技术成熟、工艺流程较为简单、系统可靠性高;脱硫率可达到80%以上,但吸收剂利用率较低(50~65%);脱硫灰渣可用作制砖、筑路,但多为抛弃至灰场或回填废旧矿坑。
3、炉内喷钙加尾部烟气增湿活化脱硫
3.1工艺原理
在炉内喷钙脱硫的基础上在锅炉尾部增设了增湿段。将石灰石粉磨用压缩空气喷射到炉内,使石灰石与烟气有良好的接触和反应时间,石灰石受热分解成氧化钙和CO2,与烟气中SO2反应生成亚硫酸钙和硫酸钙,最终被氧化成硫酸钙。尾部烟气经一特制的活化器,喷水增湿与未反应的氧化钙遇水反应生成的低温下有很高活性的Ca(OH)2,Ca(OH)2与烟气中剩余反应,最终生成硫酸钙等稳定的脱硫产物。
3.2主要反应过程
CaCO3=CaO+ CO2 CaO+SO2+1/2O2=CaSO4
CaO+H2O=Ca(OH)2 Ca(OH)2+SO2+1/2O2=CaSO4+H2O
3.3工艺特点
能以合理的钙硫比得到中等甚至较高的脱硫;工艺流程简单,占地面积小,费用低;适用于新建大型电站锅炉及小型工业锅炉和现役锅炉脱硫技术改造;吸着剂为石灰石等钙基物料,资源分布广泛,脱硫产物为中性固态渣,无二次污染;整个脱硫系统可单独操作,解列后不影响锅炉的正常运行。
4、烟气循环流化床脱硫
4.1工艺原理
由吸收剂制备、吸收塔、脱硫灰再循环、除尘器及控制系统等部分组成。一般采用干态的消石灰粉作为吸收剂,也可采用其它对二氧化硫有吸收反应能力的干粉或浆液作为吸收剂。烟气从底部通过文丘里管进入循环流化床吸收塔内。在文丘里管出口扩管段设一套喷水装置,并在此与很细的吸收剂粉末互相混合,形成流化床,吸收剂与烟气中的二氧化硫反应生成CaSO3和CaSO4。脱硫后携带大量固体颗粒的烟气从吸收塔顶部排出,进入再循环除尘器,被分离出来的颗粒经中间灰仓返回吸收塔。
4.2主要反应过程
Ca(OH)2+SO2=CaSO3·1/2H2O+1/2H2O
Ca(OH)2+SO3=CaSO4·1/2H2O+1/2H2O
CaSO3·1/2H2O+1/2O2=CaSO4·1/2H2O
Ca(OH)2+CO2=CaCO3+H2O
4.3工艺特点
脱硫效率高达95%以上;工艺简单,操作方便,系统可靠性高;烟气无需再加热;脱硫副产物为干态,无废水产生;占地面积小、投资省、维护费用低。
5、氨水洗涤法脱硫
5.1工艺原理
在吸收塔内,氨水或液氨与烟气接触混合,洗涤后的烟气经过液滴分离器除去水滴进入前置洗涤器中。吸收液自塔顶喷淋洗涤烟气, SO2被洗涤吸收除去,经洗涤的烟气排出后经液滴分离器除去携带的水滴,进入脱硫洗涤器。在该洗涤器中烟气进一步被洗涤,经塔顶的除雾器除,进入脱硫洗涤器。再经烟气换热器后经烟囱排放。
5.2主要反应过程
SO2+(NH4)2SO3+H2O=2NH4HSO3
NH3+NH4HSO3=(NH4)2SO3
2(NH4)2SO3+O2=2(NH4)2SO4
5.3工艺特点
脱硫效率高达98%以上;系统能耗低;对煤种变化、负荷变化的适应性强,适用于高硫煤;副产品回收的经济效益高;具有一定的脱硝功能。
结论
随着我国新的大气排放标准的逐步颁布实施,对烟气脱硫提出的要求越来越高。为满足环境空气质量要求,必须采用切实可行的脱硫措施及改造方案,降低SO2的排放浓度。通过对以上几种烟气脱硫工艺的比较,在选择烟气脱硫工艺时应结合当地实际情况进行充分论证,进行合理化利用。
参考文献
[1]刘天齐主编.三废处理工程技术手册 ( 废气卷)[M].北京:化学工业出版社
脱硫工艺论文篇11
概述:
目前,城市的生活和工作环境污染越来越严重,人们对环境保护要求也不断提高,尤其是对二氧化硫的排放浓度和排放量严格控制后,烧结烟气脱硫技术逐渐引起了企业的重视。从发电厂锅炉烟气脱硫技术的应用经验来看,成熟的技术主要有干法和湿法两种。干法的主要代表有循环流化床工艺、密相干塔工艺、NID工艺;湿法的主要代表有石膏法、氨法脱硫工艺与镁法脱硫工艺。烧结烟气脱硫技术也主要以这两种脱硫工艺为主,两种工艺在国内钢铁企业烧结机中的应用实例技术参数见表2。
表2湿法脱硫、半干法脱硫技术参数
干法与湿法两种脱硫工艺均有比较明显的优缺点: 干法脱硫工艺投资小、占地面积小、运行费用低,但也有运行不稳定, 脱硫效率不高的弊端。湿法脱硫工艺占地面积大、投资大、容易腐蚀,但运行稳定、脱硫效率高。本文主要针对湿法烟气脱硫技术中LS氨法技术进行介绍。
2、LS氨法脱硫技术特点
在实际应用过程中逐步进行改进。LS氨法脱硫技术是在不断的探索之后形成的成熟氨法脱硫技术, 已经在锅炉烟气的治理中得到了非常广泛的应用。LS氨法脱硫反应原理属于瞬时反应, 具有多种功能,既能脱硫、脱硝, 又能除尘, 在系统流程上采用循环密闭系统, 并设有防氨泄露安全等有效措施。具体技术特点:(1)脱硫效率高。在脱硫塔内, 氨水与烟气充分接触, 属于气- 液反应, 瞬时完成, 相同反应条件下, 反应速率是最快的。(2) 副产物易于回收利用, 具有很好的应用价值。可以应用作农业肥料, 用来加工成复合化肥,或用于化工企业的原料。(3) 多功能一体化。具有良好的脱硫和除尘功能, 还具有一定的脱硝功能。(4) 液气比值小。与传统的石灰石- 石膏法脱硫技术相比, 液气比值是石灰法的1P10以上, 可以大大减少自身水、电消耗 , 减少设备总投资与运行成本。(5)脱硫反应温度区间可变范围大。在40 ~ 180 E反应塔内,脱硫效率可达95%以上。有效控制形成液的pH值,从而降低了设备的腐蚀。且循环液的温度与硫酸铵溶解度成正比,在循环液的浓度接近饱和结晶的一般控制操作,使其塔外结晶,有效避免堵塞。(6)适应烟气量和烟气含硫量的变化。脱硫系统具有较高的可靠性及灵活性, 当烟气量发生变化时,控制系统自动及时进行脱硫剂浓度和量调节。当脱硫剂浓度增加时, 系统采用独特的结构设计有效防止气体氨的释放。避免脱硫剂的浪费,同时也避免造成环境污染。(7)适应烟气中粉尘含量的变化。系统具有高效除尘功能, 烟气中粉尘在脱硫塔内得到有效收集, 同时系统中设置了固液分离装置, 有效实现粉尘的回收再利用, 也避免了系统内粉尘杂质沉淀和堵塞。(8)系统阻力小。由于LS塔属于喷射塔, 塔本体阻力比填料塔阻力小。经过塔本体阻力计算以及多次实际应用, 测试证明LS塔本体阻力均小于1000Pa, 一般在500~800Pa。
3、方案分析
3.1 项目概述
某钢厂66m2烧结机烟气脱硫工艺方案, 单台烧结机的烟气量为297000m3Ph, 烟气中二氧化硫含量设计值为2500mgPm3, 烟气中粉尘含量为200mgPm3。项目建成后, 二氧化硫的排放浓度小于100mgPm3, 粉尘排放浓度小于50mgPm3。每年可以减少二氧化硫排放7171t, 减少粉尘排放448t, 能够生产硫铵产品1140000t。
3.2 工艺路线
本项目采用LS氨法脱硫工艺。此工艺具有脱硫效率高、节省投资、运行费用低等优点。脱硫除尘后能够达到国家最新的钢铁工业污染物排放标准和清洁生产标准 ,采用单台烧结机配套一套烟气脱硫装置。具体的工艺过程主要包括:(1)氨水储存输送系统。根据钢铁厂的实际情况,可以应用其钢铁公司焦化厂的剩余氨水。用量不足的部分, 可以进行外购, 用罐车输送至厂区氨水储存系统中, 进行调氨处理以备工艺应用。(2)烟气系统。通过新增压风机引出烧结烟气,烟气经烟道至脱硫塔。在原有烟囱前和脱硫塔前分别设置挡板门, 用于烧结机运行期间脱硫装置的隔断和维护。FGD配置一台用于克服自身阻力的增压风机, 以保证烧结机的正常运行。新配置的增压风机选型要与烧结系统压力、流量等参数相匹配, 进而保证脱硫系统不影响烧结系统的正常稳定运行, 同时在烧结工况发生变化的情况下, 保证脱硫系统正常运行和脱硫除尘指标的达标。烟道要设置保温, 防止烟气温度低于酸露点对烟道产生腐蚀。(3)脱硫吸收系统。调配一定浓度的氨水, 通过喷雾反应段, 与烟气中的SO2 充分反应, 生成亚硫酸铵溶液, 流入循环液池。亚硫酸铵溶液氧化风机的不断充氧氧化为硫酸铵溶液。脱硫吸收塔内部有特殊结构设置, 用于捕集粉尘、以及可能的逃逸气溶胶。在脱硫塔底部设有循环泵, 用于吸收液的循环泵, 循环泵为离心泵, 叶轮由防腐耐磨材料制成。(4) 工艺水及废水处理系统。从烧结厂厂区供水系统引接至FGD, 分别接至工艺水箱及部分用水点。本工艺没有废水排放,氨水需要用水来调配一定浓度;在脱硫过程中会由于烟气的显热, 焓差使水蒸发损耗要补充的水。清洗塔内设备工艺水分两路: 一路送到工艺系统, 另一路送到水池补水, 所有工艺水不外排, 循环使用, 整个系统中只有补水, 没有排水。所有水量均由控制系统进行控制。(5) 脱硫副产物硫酸铵提取系统。从脱硫塔底部洗涤下来的粉尘进入洗涤液中, 并进入沉降池内, 在沉降池内通过泵送, 进入压滤机, 压滤后得到泥饼和清液。泥饼通过汽车运输到烧结原料场, 回收用作烧结原料, 以便回收其中的有用金属;清液通过泵送进入循环池内, 循环用于烟气脱硫系统。该系统装置不造成固废排放和污水排放。从曝气氧化池中由泵送来的硫酸铵溶液进入到脱硫副产物硫酸铵提取系统。鉴于烧结烟气中含有重金属可能造成脱硫副产物质量的影响, 本系统设计有重金属处理备用系统。以便于符合今后国家对烧结烟气重金属处理要求及农用化肥中重金属含量要求。
烧结烟气脱硫系统, 有以上分系统组成, 具体的流程如图1。
图1工艺流程
治理前后污染物排放对比
目前现场并没有进行烟气脱硫的治理, 该工程建成后将会在很大程度上降低烧结机的污染状况, 项目投产前后的污染物排放对比见表2。
表2 投产前后的污染物排放对比
烟气脱硫工艺选择依据
脱硫工艺论文篇12
一、烟气脱硫的方法
(一)干式烟气脱硫工艺
该工艺用于电厂烟气脱硫始于80年代初,与常规的湿式洗涤工艺相比有以下优点:投资费用较低;脱硫产物呈干态,并和飞灰相混;无需装设除雾器及再热器;设备不易腐蚀,不易发生结垢及堵塞。其缺点是:吸收剂的利用率低于湿式烟气脱硫工艺;用于高硫煤时经济性差;飞灰与脱硫产物相混可能影响综合利用;对干燥过程控制要求很高。
(二)喷雾干式烟气脱硫工艺
喷雾干式烟气脱硫(简称干法FGD),最先由美国JOY公司和丹麦NiroAtomier公司共同开发的脱硫工艺,70年代中期得到发展,并在电力工业迅速推广应用。该工艺用雾化的石灰浆液在喷雾干燥塔中与烟气接触,石灰浆液与 反应后生成一种干燥的固体反应物,最后连同飞灰一起被除尘器收集。我国曾在四川省白马电厂进行了旋转喷雾干法烟气脱硫的中间试验,取得了一些经验,为在200~300MW机组上采用旋转喷雾干法烟气脱硫优化参数的设计提供了依据。
(三)粉煤灰干式烟气脱硫技术
日本从1985年起,研究利用粉煤灰作为脱硫剂的干式烟气脱硫技术,到1988年底完成工业实用化试验,1991年初投运了首台粉煤灰干式脱硫设备,处理烟气量644000Nm3/h。其特点:脱硫率高达60%以上,性能稳定,达到了一般湿式法脱硫性能水平;脱硫剂成本低;用水量少,无需排水处理和排烟再加热,设备总费用比湿式法脱硫低1/4;煤灰脱硫剂可以复用;没有浆料,维护容易,设备系统简单可靠。
(四)湿法FGD工艺
世界各国的湿法烟气脱硫工艺流程、形式和机理大同小异,主要是使用石灰石(CaC3)、石灰(CaO)或碳酸钠(Na2CO3)等浆液作洗涤剂,在反应塔中对烟气进行洗涤,从而除去烟气中的SO2。这种工艺已有50年的历史,经过不断地改进和完善后,技术比较成熟,而且具有脱硫效率高(90%~98%),机组容量大,煤种适应性强,运行费用较低和副产品易回收等优点。据美国环保局(EPA)的统计资料,全美火电厂采用湿式脱硫装置中,湿式石灰法占39.6%,石灰石法占47.4%,两法共占87%;双碱法占4.1%,碳酸钠法占3.1%。世界各国(如德国、日本等),在大型火电厂中,90%以上采用湿式石灰/石灰石-石膏法烟气脱硫工艺流程。
石灰或石灰石法主要的化学反应机理为:
石灰法:
石灰石法:
其主要优点是能广泛地进行商品化开发,且其吸收剂的资源丰富,成本低廉,废渣既可抛弃,也可作为商品石膏回收。目前,石灰/石灰石法是世界上应用最多的一种FGD工艺,传统的石灰/石灰石工艺有其潜在的缺陷,主要表现为设备的积垢、堵塞、腐蚀与磨损。为了解决这些问题,各设备制造厂商采用了各种不同的方法,开发出第二代、第三代石灰/石灰石脱硫工艺系统。湿法FGD工艺较为成熟的还有:氢氧化镁法、氢氧化钠法、美国DavyMckee公司Wellman-LordFGD工艺、氨法等。
在湿法工艺中,烟气的再热问题直接影响整个FGD工艺的投资。因为经过湿法工艺脱硫后的烟气一般温度较低(45℃),大都在露点以下,若不经过再加热而直接排入烟囱,则容易形成酸雾,腐蚀烟囱,也不利于烟气的扩散。所以湿法FGD装置一般都配有烟气再热系统。目前,应用较多的是技术上成熟的再生(回转)式烟气热交换器(GGH),而GGH价格较贵,占整个FGD工艺投资的比例较高。前德国SHU公司开发出一种可省去GGH和烟囱的新工艺,它将整个FGD装置安装在电厂的冷却塔内,利用电厂循环水余热来加热烟气,运行情况良好,是一种十分有前途的方法。
二、烟气脱硫产物应用
(一)注意产物稳定
在脱硫的过程中,一定要注意拉引量的稳定、燃料性能的稳定以及燃料的添加大的问题等,还要稳定住脱硫时烟气的输入量,保证整个脱硫过程的稳定,增加过程的效率,这样做才能使烟气经脱硫后所得到的产物状态更加稳定。
(二)制作脱硫石膏
烟气经过脱硫后的副产物可以通过加工制作出能被建筑业应用的脱硫石膏,其中包括建筑石膏,其是由二水脱硫石膏在不饱和水蒸汽中经130℃高温脱水后,干燥制成的;高强石膏,它是由二水脱硫石膏在饱和水蒸汽中经过150℃高温脱水后,干燥制成的;粉刷石膏,这种石膏是在常规石膏的起初上混合了30%到70%的脱硫石膏制成的;还有其它的建筑材料,诸如:卫生间、通风道内的瓷砖、建筑的内墙和棚顶以及保温材料等。这些建筑材料在建筑工程施工过程中有着很大的作用,也可有效节约成本。
(三)用于农业领域
经过脱硫后所得到的副产物还可以运用到农业领域,可以被制成化肥,也可以改善土质。在我国农业中,对于氮肥的施用存在着严重过度现象,导致了植物对硫元素的吸收不够,而经过脱硫处理后得到的副产物中含有大量的以硫酸铵和硫酸钙形式存在的硫元素,这些硫元素不但可以为作物施加硫肥,使作物的营养比例均衡,而且在施用硫肥的过程中国也使得土壤的酸碱度发生了变化,尤其有利于我国北方的黑土地这种碱性过高的土质。
三、结论
对烟气进行脱硫工作不但可以改善我国现有的空气质量,而且还可以对脱硫后产生的副产物进行回收再利用,节约了国家的资源,减小了相关产业的成本,提高了环保工作的效率。它是一种值得在中国推广应用的好方法。
参考文献
[1]杜.单碱法在剥离工厂烟气脱硫处理中的应用于探讨[J].建材世界,2009(2)
脱硫工艺论文篇13
SO2是大气中主要污染物之一,而大气中的SO2气体80%以上都来自于各类燃煤设备,所以降低燃煤设备的SO2排放量,对于改善生态环境具有重要意义。近二十多年来,一些发达国家就降低燃煤设备的SO2排放量,进行了大量试验和研究,其中有些技术已在实际中得到推广和应用。炉内喷钙脱硫技术就是其中一种,炉内喷钙是指直接将钙基脱硫剂喷入炉膛热烟气中,与其中的SO2发生反应进行脱硫的技术。该项技术投资少,运行费用低,不产生废水,但是由于反应较难充分进行,大量未反应的脱硫剂都随烟气离开了炉膛,因此其脱硫率和脱硫剂的利用率都很低,不能满足日益严格的锅炉要求。因此人们在此基础上进行改进,开发了多种新型的炉内喷钙类脱硫技术,炉内喷钙尾部增湿脱硫技术LIFAC就是其中的一种。
2 炉内喷钙脱硫的理论分析
石灰石的热解特性:石灰石在700~800℃时开始缓慢热解,在850~950℃时热解反应加快,在低于700℃和高于950℃的恒温时均不发生热解。石灰石的这种热解特性是脱硫的重要依据,炉内喷钙脱硫选择在燃烧室上部区域(温度在850~1100℃)喷入石灰石粉末就是根据这一原理。这里之所以将烟温高限增至1100℃,主要是考虑到运行条件(如煤种、石灰石品质、负荷等)的变化。试验证明即使保持烟温在850~950℃恒温下,石灰石热解产物的脱硫时间也需要持续60~70min才能完全完成,但锅炉烟气从燃烧室出口到除尘器前远不可能有这么长的时间,故需要在尾部再设置增湿活化反应器,采用雾化水枪将少量水雾化,进一步提高烟气除硫。
3 脱硫工艺流程
该工艺多以石灰石粉为脱硫剂,石灰石粉由气力输送的方式喷入炉膛中的850~1150℃温度区域,石灰石受热后其分解产物氧化钙与烟气中SO2反应生成亚硫酸钙。由于反应在气固两相间进行,受到传质速度的影响,反应速度较慢,吸收剂利用率较低。炉内喷钙后的脱硫率随煤种、石灰石粉的特性、炉型及炉内空气动力场和温度场等因素的变化而改变,一般为20~50%。
在尾部增湿活化反应器内,增湿水以雾状喷入,与未反应的氧化钙接触生成反应活性更高的氢氧化钙,进而与烟气中的SO2、SO3反应。活化器内的脱硫率取决于雾化的水量、液滴的粒径分布、烟速以及出口烟温等因素,一般为40%~60%。在采用底灰再循环时,可以使整体脱硫效率接近90%。
由于在烟气中喷入增湿水,使烟气温度下降,增湿水由于吸收烟气热量而被迅速蒸发,未反应的脱硫剂、反应产物呈干态随烟气排出被除尘器收集下来,不产生废水。脱硫产品中亚硫酸钙含量较高,其进一步的综合利用受到限制。
4 技术特点
(1)如同湿法烟气脱硫工艺一样,可以采用石灰石作为脱硫剂,具有资源分布广泛,价格低廉,处理简便等特点。(2)系统工艺流程简单,占地面积小,无废水排放,初投姿低,运行费用较低,并能得到较高的脱硫效率。(3)既适用于新建大型电站锅炉及中小型工业锅炉,又适用于现役锅炉增设脱硫装置的改造,不需另设单独脱硫风机,增加的阻力完全可以由锅炉的引风机克服。(4)脱硫副产品的成分与喷雾干燥工艺相似,脱硫灰渣为干态,为稳定的中性物资,但是,它包括了更多的飞灰(70%~80%),石灰的含量也较高。脱硫产品一般采取堆放处理,但要考虑堆放对地下水的影响。(5)活化反应器的底渣和除尘器下的部分灰再循环使用,有利于提高脱硫效率和脱硫剂的利用率。(6)脱硫系统与电站机组、尤其是锅炉的运行关系紧密。由于在炉膛内喷入脱硫剂,会对锅炉的工作产生程度不同的不利影响,存在造成锅炉炉内受热面结渣。加剧受热面磨损的可能性。(7)由于脱硫系统启动迅速,因此,对锅炉负荷的变化有良好的跟踪能力。(8)脱硫系统的投运将使锅炉尾部排出的粉尘量成倍增加,因此,需要增加除尘器的设计出力或改造现有的除尘器,以保证除尘效果。
参考文献:
[1]阎维平.洁净煤发电技术.北京:中国电力出版社,2002.
[2]姚强等.洁净煤技术.化学工业出版社,2005.
[3]赵旺初.电站锅炉炉内喷钙脱硫简介.锅炉技术,1998.
[4]刘寅洁.LIFAC脱硫新工艺.环境保护,1992.
[5]董文刚,侯栋歧,于德亭.喷钙脱硫成套技术.锅炉技术,1999.
[6]杨吉青,周俊虎,程军等.煤粉炉喷钙脱硫技术.中国电力,2005.