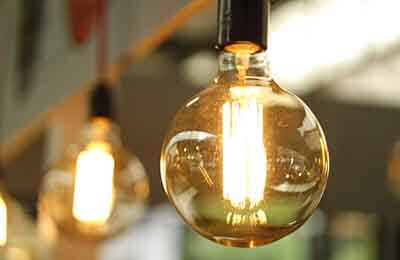
电气控制论文篇1
“机电产品电气控制”课程采用自编教材。教材的编写紧密结合实现技能型人才培养目标,从内容选材、教学方法、学习方法、实训配套等方面突出高职教育的特点,突出应用能力培养的特点,摆脱理论分析长而深的模式,增加并充实应用实例的内容,对职业岗位所需知识和能力结构进行恰当的设计安排。在知识的实用性、综合性上多下功夫,理论联系实际,加强操作与实训,把学生应用能力培养融汇于教材之中,并贯穿始终[3]。在内容组织上,以符合教学要求的工作过程为基础,由简单到复杂,由单一到综合,层层递进,将职业岗位所需的理论知识系统的串在一起,教材内容基本涵盖了基本电气控制规律、机床电气控制系统,PLC控制系统的组成。由浅入深,由易到难,每个部分都有实践训练,指导学生能够主动学习、提高效率,动手能力能够得到逐步提高。在教材编排上,打破以往教材先理论后实践的编写模式,以典型工作任务和任务的完整性及为主线,以提高职业能力为线索,理论知识够用为度编排教材内容。教材共有与《课程标准》内容相一致的八个学习项目,根据项目理论知识要求,将项目分解成各个子任务,每个子任务都有自己独立的知识点和训练内容,完成了子任务的学习,也就完成了整个项目的学习,并能使知识融会贯通。编写教材时充分体现“以学生为中心”“教中学,学中做”的职业教育理念,强调以学生直接经验形式掌握融于各项实践行动中的知识和技能,以学生能力培养为本位。
三、教学方法的改革
树立以学生为主体,教师为主导的教学理念。学习不仅是为了获取技术,还需要在获取技术的活动中,培养学生的方法能力、社会能力,使学生不仅要有技术适应能力,更重要的是有能力对社会、经济负责的态度,参与设计和创造未来的技术和劳动世界,因此在教学过程中注重强调教师对学生引导的行为。针对不同的教学实施环节,我们选用了不同的教学模式。1.教、学、做一体化教学模式教、学、做一体化教学模式是一边进行知识讲解和操作示范,一边让学生进行课程同步训练,符合学生认知规律。将知识点溶解到任务的实现中,完成学生对知识的理解和应用,能循序渐进地使学生最大限度地掌握知识。教、学、做三者融合,“教”为指导,“学”为过程,“做”为中心。学生在学了以后立即实施,实施完毕再进行总结,加强了对理论知识的掌握程度,巩固了知识在脑海中的印象。教、学、做一体化教学模式有利于学生利用教学软件、仿真软件等课程资源解决课程疑问,提高学习主动性。2.项目引导,任务驱动化教学模式项目引导,任务驱动化教学模式是在校内维修电工实训室、机床电气实训室及PLC实训室完成。围绕“控制线路的设计、安装、调试和运行维护”这一学习情境,把工作过程分成了8个项目,采取项目引导任务驱动,一步一台阶引导学生自主完成基本电气控制线路、机床电气、PLC综合技能实训领域的学习过程。在完成职业活动的学习过程中,也逐步训练和培养了学生系统的工作方法和严谨的工作作风,培养了学生具有良好的职业道德、团队协作能力与沟通能力和较强的工作责任心。教学过程贯彻“学生主体,教师主导”的原则,从教师指导学习教师引导学习学生自主学习。教师的指导作用逐步减弱,学生的主体作用逐步加强[4]。3.基于网络资源的自主学习这种方法突破了时空的限制,通过网络教学将学习延伸到课堂之外。我们将课程教学课件、实训课件和PLC编程软件与仿真软件挂接到课程网站。很多时候,学生在课堂实践中并不能通过一两次的模仿操作就可以理解操作要领和知识点的,少数学生不能独立及时完成一次完整的操作任务。因此,反复练习是提高理解和掌握技能的重要手段。
四、评价体系的改革
实践考核更注重学生的工作过程、职业素养,而非结果。同时,把学生的平时操行纳入考核的范围,对平时表现突出的优秀学生,给予加分;纪律及学习态度不好的,酌情减分。采取以过程考核为主的多元化考核方式的各部分考核所占的比例如下:职业素质考核方法:沿纵向以项目为单元,逐项考核。即在学生完成每个项目的工作任务和实操训练之后,对学生完成该项目的工作任务过程中的能力给予评价和认定。当本课程全部项目的工作任务和实操训练完成后,将各项目考核成绩累加。横向重点考核学生能力发展的渐进过程,即随着学习内容的扩展,评价学生完成工作任务的质量、合作能力及个人素质等,将纵向和横向的考核成绩按比例综合,即为学生学习本课程的最终成绩。
电气控制论文篇2
《电气控制与PLC》作为一门职业岗位特征十分明显的课程,传统的知识系统型课程已经难以适应该课程的教学要求,迫切需要按照工作过程导向进行该课程的开发.根据此课程的特点,工作过程导向的《电气控制与PLC》课程开发过程如图2所示.在课程开发过程中,通过专任教师与不同合作对象的配合,使其能够与该课程对应的工作过程零距离,使所承担的教学活动能够培养出胜任工作岗位的合格工作者.(1)在岗位能力调研阶段,通过任课教师通过到企业与工程技术人员一起进行实地调研,明确《电气控制与PLC》所对应的工作岗位是维修电工,该工作岗位具体需要的核心技术能力为机电设备电气控制安装与维修.(2)在岗位任务分析阶段,任课教师与行业专家一起具体分析课程对应的维修电工岗位典型的工作的任务,也为课程内容选取和学习情景的构造积累素材和奠定基础.(3)在课程结构组织阶段,任课教师在职教专家的指导下对与本课程相关的其他课程进行整合,避免教学内容遗漏与重复.(4)在课程内容选取阶段,任课教师根据前面确定的岗位能力、岗位任务以及课程整合的结构,在岗位能手的协助下选取本课程具体的内容,同时也将学习情境构造完成.(5)在教学活动实施阶段,任课教师与学生在构造的学习情境下完成预定的教学任务.(6)在教学完成后,任课教师在教育专家的指导下对本课程的教学质量进行评估,并提出改进意见,促进今后的课程建设工作.
电气控制论文篇3
论文摘要:电路图是电气线路安装、调试与维修的理论依据。对任何复杂的电路图,若有了正确的识图思路是不难掌握其工作原理的。 论文关键词:电路;回路;电路图;识图思路 电路图能充分表达电气设备的用途、作用和工作原理,是电气线路安装、调试和维修的理论依据。在生产实践中,安装电工与维修电工等人员都要接触到各种各样的电路图。这些电路图有的比较简单,有的很复杂。笔者在多年的教学实践中积累了一些识图经验。 先识机,后识电先识机,就是应该先了解生产机械的基本结构、运行情况、工艺要求和操作方法,以便对生产机械的结构及其运行情况有总体了解。后识电,就是在识机的基础上进而明确对电力拖动的控制要求,为分析电路做好前期准备。例如,在给学生讲解识读国产CA6140型普通卧式车床电路图时,笔者先组织带领学生到工厂或实习车间参观各种型号的普通卧式车床,让学生了解车床是由床身、主轴箱、进给箱、溜板箱、刀架、丝杠、光杠、尾架等部分组成的。对车床的结构了解后,再让学生知道车床的运动形式,使学生明确主轴带动工件的旋转运动是主运动,车刀的直线运动是进给运动。机动进给运动也是由主轴电动机经过主轴箱传给进给箱,再通过光杠或丝杠将运动传入溜板箱,溜板箱带动刀架作纵横两个方向的进给运动。这时,教师可以将拖板用手移动到床身的最右边,并提出问题:这样操作效率是否太低了?学生回答之后,教师再告知学生:为了提高劳动生产率,减少辅助时间,设置了刀架快速电动机。教师可以给学生演示刀架的快速移动是由快速电动机点动控制的,刀架运动的方向由操作手柄控制。通过这种方式可使学生产生好奇心,从而激发求知欲望。在车削加工时,由于刀具及工件温度过高,有时需要冷却,因而应该配有冷却泵电动机。教师应该在全面演示车床的操纵过程后,再指导部分学生进行车床操纵练习。学生对CA6140型车床的基本结构和运行情况了解后,对电力拖动的控制要求就明确了。教师可以先让学生回答电力拖动的特点和控制要求,然后再给出答案。在讲解Z37型摇臂钻床、M1432A型万能外圆磨床及X62W型万能铣床等各种机床电路图时,应先组织带领学生到工厂和实习车间去参观、了解各种机床的结构组成,让学生知道各种机床的运动形式。必要时还可以让学生进行简单的操纵练习。这样,学生就能够明确各种机床电力拖动的控制要求了。然后,教师在课堂上讲解各种机床电路的工作原理。这种教学模式可以使学生明确识图思路,很容易读懂电气控制电路图,从而提高识图能力。 先识主,后识辅先识主,就是从主回路开始识图。首先,要看清楚设备由几台电动机拖动,各台电动机的作用,结合加工工艺分析电动机的启动方法,有无正反转控制,采用何种制动方式。其次,要弄清楚用电设备是由什么电气元件控制的。有的用刀开关控制,有的用接触器或继电器控制。再次,了解主电路中其他元器件的作用,通常主电路中除了用电器和控制用的接触器与继电器外,还有电源开关、熔断器及保护电器。最后,看电源。看主电路电源是380V,还是220V。主电路电源是由母线汇流环供电或配电屏供电的。后识辅,就是识读辅助电路时应从主电路入手,根据每台电动机、电磁阀等执行电器的控制要求去分析它们的控制内容。控制内容包括启动、方向控制、调速控制和制动控制等。由于有各种不同类型的生产机械设备,其电路图中的辅助电路也各不相同。辅助电路包含控制电路、信号电路和照明电路。例如,笔者在给学生讲解国产X62W型万能铣床电路图时,也是先组织学生到工厂或实习车间了解铣床的结构组成、运动形式,让学生明确了电力拖动控制要求。回到课堂后,再给学生讲解电路工作原理。教师应具备在黑板上绘图的能力。例如,根据铣床的控制要求,引导学生进行主电路的识读。主电路共有三台电动机:(1)M1是主轴电动机,拖动主轴带动铣刀进行铣削加工,由KM1接触器控制启动
电气控制论文篇4
(一)免去了控制模型的建立
在电气工程的传统工作中,自动化系统控制的实现必须有控制模型的建立。但是,在实际的操作中,被控制对象往往需要十分复杂的动态方程,这就影响了精确效果的获得。由此,在设计对象模型的环节中,经常会遇到无法科学预测、无法准确估量的一系列困难。然而,智能化系统的出现,使这些困难得到了较好解决,极大促进了工作效率的提升,同时对于一些不可控制的因素,也实现了较好的控制,大大提升了自动化控制器的准确性。
(二)实现了便捷的电气系统控制
智能化控制器的实际应用实现了更加便捷的电气系统控制,随时都可以完成对系统控制程度的有效调整,极大提升了系统的整体工作性能,是对自动化控制顺利实现的进一步保障。从这一项优势中就可以看到,和传统的自动化控制器相比较,在任何条件下,智能化控制器都具有更加完善的调解控制功能,在电气工程的自动化实践应用中占据优势。
(三)实现了一致性的智能化控制
在自动化控制中的数据处理环节,智能化控制器可以实现一致性的智能化控制,很好解决了不同数据的处理困难。而且,在自动化控制的标准执行上,即使遇到陌生的数据,也依旧可以获得具有较高准确度的估计。但是,如果发现智能化控制器在实际的应用中没有发挥出理想的效果,一定要全面排查工程的各个细节,细致地进行分析,不能盲目的否定智能化控制技术。
三、智能化技术的实践应用
(一)系统病因诊断
在电气工程诊断工作中,采用传统的人工手段具有较强的复杂性,虽然对工作人员要求十分严格,但是也无法获得较为准确的诊断病因。在电气工程工作中,实现自动化控制的过程中经常会遇到一些如设备、数据等方面的问题,这是不可能避免的,采用传统的人工诊断办法不能确保病因处理的及时性,而且处理效果也不佳。但是,智能化技术的广泛应用,使得自动化控制工作的诊断效率得到大幅度提升。而且,定时检测诊断应用,有效避免了一些不必要的问题。
(二)系统设计优化
在电气工程发展中,传统的工程设计需要工作人员进行多次重复的实验操作和改良,而且,在这一工作过程中,对工作人员的工作素质也有着较高的要求,既需要工作人员掌握一定的专业设计知识,还需要工作人员能够很好的将知识理论应用于实践工作中。但是,在实际的设计工作中,工作人员往往不能做到全面的考虑,经常会漏掉一些具体的问题。所以,一旦发现复杂问题,很多情况下都不能做到及时解决。而智能化技术的出现,较好解决了这一问题。设计工作可以借助于计算机网络完成,也可以借助于相关的软件完成,既保证了设计中数据的准确性,也实现了设计样式的丰富化,更能够做到对复杂问题的及时处理,较好保证了自动化控制的稳定性。
(三)系统的自动化控制
在电气工程中,智能化技术可以应用于多个控制环节,能够很好的实现整体性的自动化控制。智能化技术的主要控制工作是借助于三种手段实现的,一是模糊控制,二是专家系统控制,三是神经网络控制。运用这三种控制手段,极大提升了自动化控制效率,使远距离的自动化控制成为可能,增强了对电气系统的运行反馈。特别是神经网络控制,能够实现算法的反向学习,在信号处理方面得到了较大应用。
电气控制论文篇5
3.素质目标:遵守学校管理规定,引入企业8S管理(整理/整顿/清扫/清洁/素养/安全/节约/学习),填写、整理、积累技术资料等,培养学生的文明习惯、团队意识、语言表达能力、资料收集和整理能力等。
二、课程模块
本课程基于工作过程、以项目为导向、以工作任务为驱动、突出学生专业能力和职业素养的培养。在课程设计中,首先以企业调研和毕业生回访为依据,得出相关的职业岗位,然后进行岗位能力分析,归纳提炼出典型工作任务,最后将工作任务转化为课程学习内容。另外,在课程设计中,我们始终贯穿以“能力和素养并重”为主线,以培养高素质技能型人才为出发点,以满足岗位职业要求为目标,以真实的工作任务为载体,以必需够用来设计教学内容,并将课程内容与相关的职业资格技能培训和鉴定相互贯通。据此。本课程内容整体设计为8个项目。
三、教学方法与教学手段
1.项目分析法:以项目为着手点,分析归纳出完成的任务和要求,然后对所需知识和技能进行讲解、引导、训练,学生容易接受,并且教学效果好。
2.任务驱动法:以实现具体任务为目标,让学生如何一步步地完成任务,从而让学生观察、思考、讨论等,并制定实施方案。例如现需要完成PLC控制系统,先分析控制要求、I/O如何分配、系统的软硬件如何设计、元器件如何选择、如何安装调试及撰写任务书等。
3“.教、学、做”合一:通过教师的演示、学生训练及教师指导相结合,帮助学生提高专业技能及素养,并在做的过程中掌握相关理论。
4.小组讨论法:针对实践教学中的方案和问题积极进行讨论,并得出结论,从而来提高学生团结协作、沟通表达的能力。
5.引入现代信息技术:建立课程网站,给学生提供更多的图片、视频、试题、新闻等资料,来激发学习兴趣,调动学习积极性,提高教学效果。
四、课程考核
实施了以“能力和素养并重”的过程考核,在考核评价标准及方式上不再以期末考试为主,而是在理论测试的基础上增加技能考核项目,同时注重学生素养的培养,从而构成了“素养、技能、知识”三位一体的考核评价模式。将平时教学工作任务的完成情况,作为考核评价的重要组成。在考核形式上,改变了以往一味的结果评价,侧重过程化考核。在该课程能力考核中,是否完成工作任务,并不是考核的唯一依据,而是同时考虑在完成任务的过程中,是否有适合的方案、步骤及工具仪表使用情况等。总之,该课程在考核中,考虑了学生的学习态度、独立思考和创新意识、任务完成过程、学习进步情况等多方面,力求全面客观反映学生学习的效果。
电气控制论文篇6
一、电气工程的质量控制
1、施工准备阶段的质量控制
电气工程师不能只停留在按图施工的水平,要全面熟悉设计图纸,努力并善于发现图纸中的不足,及时提出处理意见,对业主而言是维护其利益,对自己也是提高。好的工程质量是由高素质高水平的施工人员完成的,这就要求施工前要对施工队伍及人员进行考核和评估,并调整好技工和普工的比例。电气工程师要根据工程的实际情况编制施工组织设计(施工技术方案)并严格审查,要求有完善的质量保证体系、保证工程质量的各项技术措施,而且应符合经会审的设计图纸及国家现行的有关电气工程的施工及验收规范。对施工班组及人员进行工程的总体技术交底,由于施工人员流动性较大,还要根据工程的进度情况分阶段进行交底。明确现行实用的规范及操作规程和顺序,对工程所需的资料表格及相关技术文件、要求、标准做到心中有数。根据业主及土建工程的总体进度编制电气工程进度计划、人员计划、机具计划并组织落实,工程过程中要根据实际情况及时修改及补充。
2、施工阶段的质量控制
施工中必须根据已会审后的电气设计图纸和有关技术文件,按照国家现行的电气工程施工及验收规范,地方有关工程建设的法规、文件,经审批的施工组织设计(施工技术方案)进行。①主体施工阶段重点注意以下几个问题:严把电气管材、线盒的质量关,将不合格材料拒之于工程之外(如镀锌钢管的壁厚,厚管不小于2.5mm,薄管不小于1.5mm,镀锌层应完好,PVC管应采用中型以上,一般采用重型管,必须是阻燃型。每次进材料都应填报审表,经监理审查同意后方能用于工程)。要特别注意胶水的质量,最好选用与线管同一品牌的胶水,一般都能符合要求,浇注砼时,要求每台输送泵都有电工跟班,及时处理被压坏的线管、线盒。均压环、避雷带、防雷引下线等对建筑的安全非常重要,是否漏焊,焊接长度及质量是否满足规范及设计要求。每处都要仔细检查,特别是结构转换层,由于柱子主筋调整,防雷引下线容易错焊、漏焊,所以电气工程师要提醒施工人员引起重视,这也是监理检查内容的重点,必须认真检查,确保工程质量。②安装及调试阶段重点注意以下几个问题:要求先对配电箱、线盒内压线做样板,布线整齐、压接牢固,多股线搪锡,然后再全面展开,防止做了大量工作后才发现存在的问题,返工困难,而且影响进度。接地线的连接,接地端子的预留应符合规范要求;外墙的金属门窗、栏杆防及屋面的金属大件部分防雷作为关键,搞好工序衔接,防止遗漏;设备外壳接地应完善。要求工作按程序进行。设备运行调试要按先空载后带负荷、先单体后联动进行;并应先对可调元件如热继电器调整至设计规定值,调试运行还要持续运行规定的时间,验证电气及机械性能的可靠性。重点检查吊顶内的线路,导线穿管敷设必须符合要求。发电机自启动、与市电切换,双电源末端切换的调试,尽管实施时比较简单,但往往因为太简单、不重视或各工种之间协调不好而出现问题。消防泵的控制,因涉及降压起动、现场手动、消防控制室手动、自动起动、备用互投等控制,且往往涉及几家安装调试(供货)单位,很容易发生技术上、协调配合上的问题,加上个别设计存在一些小缺陷,影响调试和验收,电气工程师必须提前熟悉设计图纸及厂家提供的二次线路图、控制原理图,及早发现或预见可能发生的问题,并作出处理。
总之,在施工阶段质量控制方面需注意的细节问题很多,要抓住关键点,重点检查和控制。二、电气工程的施工安全
电气控制论文篇7
1施工前对电气工程的质量控制
1.1做好对施工图纸的设计、审查,编制好施工方案
施工前要认真设计图纸,使其符合建筑设计和现场的实际情况,并与土建相关人员一起核对土建与电气的施工图纸,明确两者间的交叉检查施工部分,避免交叉部位的冲突。审阅图纸时,就建筑工程而言,要根据建筑的标准、构造及布局,和供电方式、电压等级、线路走向、铺设方式等,做出合理说明和建议。施工方案的编制,要跟施工单位商议,配合施工进度,对有关基础性部件进行预埋,如线路保护管的预埋、支撑架的预埋和基础型钢的预埋。
1.2电气设备与材料质量的控制
电气设备与各类电气材料要符合国家标准,要避免不合格产品对建筑电气的用电安全造成危害。如一些电线存在着抗腐蚀性能力差、耐热耐压性差、电阻过小的问题,空气断电器和漏电开关存在质量问题,供电设备老化和保护措施不当,这些都会严重影响建筑电气系统的正常运行,甚至引发重大的安全事故。所以一定要对电气设备及材料进行质量检查,核对出厂合格证或质量证明书,必要时,去相关检测部门进行检验,合格后方可使用。
1.3对施工人员的岗前培训和指导
要培养合格的技术人员,使其具备丰富的专业知识和一些工作经验,对施工的各个部分深入了解,对每一道工序都能严格按照要求和相关的国家标准执行。在项目开工前,技术人员应先熟悉建筑电气施工方案和设计图纸,并能同土建人员进行沟通,共同配合好建筑工程的实施。还要根据施工方案,对施工人员的工作进行分配,使其掌握自己部分的工作,并能配合整体工程,这样能管控好电气工程施工质量的人为因素。
2施工阶段的质量控制
2.1施工基础阶段
施工过程中,电气工程的质量控制更为复杂。首先,在基础施工阶段,就要做好各类工程材料的预埋工作,及时协同土建单位完成强弱电进户电缆的穿墙管道与防水板预埋、预留工作。对于预埋部件如吊卡、吊杆的基础螺栓、配电柜的基础和建筑防雷接地引下线等做好防护和焊接工作。其次,检查各个专业的配套部件的位置结构的合理性。例如敷设管线的布设,要与结构墙、吊顶位置、地面的垫层配合好,避免管线的浪费。最后,要考虑电气设备与材料的安装和其他建筑施工的部件的配置的合理性。如对给水排水管道、热力通风管道和通信布线等与电气设备的位置和配合防护都要充分考虑。
2.2施工主体阶段的质量控制
在施工主体阶段,电气施工的质量体系的建立和运行需要进行分类管理。可以从大到小,从整体到局部,先给电气工程分项,如照明工程、线路工程等,然后给各项工程再分成几个部分,如照明工程是由管具、灯具、开关、配电盘以及进外户线的安装构成。所以在主体施工前,首先,要对其涉及到施工环节的主次进行确定分类,实现各设备的交接协调,如确定电力缆线、供配电装置、配电箱三个重点设备交接配合,根据规范超前控制,达到对工程质量的预控。其次,对重点设备,尤其是影响建筑电气施工质量的因素,予以重点关注。如等电位系统必须保证良好接连,使建筑物内所有导线位置始终处于零电位,避免人们受到电击伤害;防雷接线时,尽量减少均压环、引下线及避雷带的连接处的焊瘤、虚焊等问题,防止其影响引雷效果,焊接部分也要做防锈漆处理,增加使用寿命;管线敷设要根据设计图纸和实际情况进行,避免在穿线时出现缆线太多、管道过细等问题,以免造成管线浪费,线体散热不足,影响使用,增加花费;开关、插座的安装要稳固,线盒不要埋设过深,根据用户的使用要求对开关和插座的位置调整。最后,要配合好土建施工。依据土建施工的进程与工序要求,完成管线的敷设,并给予一些保护措施,如在电线穿越楼板时,用足够长钢管加以保护;在通过伸缩缝时,埋设补偿盒,管线铺设略微宽松。浇筑混凝土时,注意对电气管道的防护,防止混凝土振捣时对管道造成损害或使其移位,影响以后电气的使用。
2.3施工装修阶段的质量控制
电气施工时,要遵循室外线管地下化、室内线路暗敷化的原则,做到隐蔽安装、美观实用的要求。在装修阶段,对于设计中的漏项和客户增加的要求,要及时补救,但不能采用重新打洞,明敷线路的办法。电气安装后,要再次检查,并且验证其使用是否正常。还要做到对成品的保护,提高人员成品保护意识,并设专人定期检查。明确各道工序每个人的责任,在验收期间,做好交接手续。
3施工后验收质量控制
制定严格的质量验收标准。严格按照设计图纸和技术规范,认真进行质量检查程序,这是对建筑电气施工质量控制的最后一道程序,必须遵循先自检、后互检、在进行交接检、隐检等。严格把握工程验收,对于管线,电线、电气设备以及固定设备连接处的各类固定材料都要进行认真检验,还要有严格的电气设备的性能测试,如严格绝缘测试、接地测试等。对于按照检验操后不合格的,要坚决不予验收,并责令施工方限期修改,这样才能保证电气施工质量的最后一道防线。
4结束语
通过上述对建筑电气工程各个程序的分析,要提高电气安装工程的质量,首先,严格把握建筑电气安装的工作要点。比如管线走向、开关和插座的位置要根据用电设备所处位置进行安装;暗线敷设时必须配备管线,以保护电线;电源线的配线要满足最大功率;电源线与通讯线不能穿在同一根管道中,管内总线根数不能超过八根等。其次,建筑电气设备与材料必须严格符合国家标准,保证安装设施的安全有效。一般要根据国家标准GB50303-2002《建筑电气工程施工质量验收》进行检验验收。最后,电气工程的施工要能配合其他建筑工程施工。这样不仅能保证建筑整体施工的顺利进行,还能保证电气施工在有些环节的质量控制。综上所述,建筑工程中的电气施工是一项复杂的工作,需要施工中各部分的规划、配合、执行。要做到对电气工程的质量控制就需对电气工程的各个程序进行监控,从一开始的工程设计、人员配备、施工准备到后来电气施工过程和后续检验都需严格按照标准,进行质量控制。通过严格的施工管理、有效的施工配合组织和高标准的质量控制,才能确保电气施工安装及使用的有效安全,从而保证建筑工程整体的安全,提高工程质量。
作者:刘 莹 单位:广州市机电安装有限公司
参考文献
[1]周峰鹿,王生云.浅谈电气工程的质量控制[J].甘肃科技纵横,2005,34:110-112.
电气控制论文篇8
工程材料、器件和设备的质量是保证工程质量的先天因素,电气质量管理人员对进场的合格材料和设备要及时填写“工程材料报验单”并附加材料清单、材质证明(检验报告),经核验,认定合格后,方可用于工程。使用实行强制管理的电工产品,必须符合中国电工产品认证委员会的安全认证要求,其电气设备上应带有安全认证标志,其生产厂家必须持有“电工产品认证合格证书”,凡未经认证的此类产品均不准使用,建筑电气工程安装的高低压开关柜及各类箱屏,须采用国家有关部门认可的定点厂家生产的产品,对于重要的关键性工程材料、器件、设备厂家的制造工艺、质量控制、检测手段、管理水平等,必要时质量管理人员应到生产厂家做实地考察,以确定最佳的供货单位,如若在电气安装施工中发现所用材料并非合格产品时,应立即停止施工,查明情况,依具体情况进行处理。在具体安装过程中,对于电气材料的各种电气性能试验(如交流耐压、直流耐压、泄漏电流试验、绝缘电阻测定、接地电阻测定等)均应按规范要求进行,对于电气设备的各项试验应按规范要求,参照出厂说明及试验报告,在安装工作中具备试验条件时与有关人员共同进行。电气质量管理人员及施工人员应正确掌握各种测试方法,对原材料、设备等通过检查和测试,准确地判断出其质量的好坏,及时发现并排除设备上影响质量的不利因素。质量检测工作是质量管理工作的主要组成部分,要改进主要凭经验目测的印象和靠检验尺等简易现场检测方式。工程交工后应通过回访,了解工程的使用效果,对于使用中出现的有关质量问题和缺陷,分析原因,总结出经验和教训,以利于今后施工质量的提高。对于较大型的电气设备还需必要的解体检验,即将设备解体后,对内部进行检验,如变压器的吊芯检查、电动机的轴心检查、油断路器的解体检查和调整等。电气质量小组应要求电气施工班组进行自检、互检和交接班检查,负责施工过程的各个环节的检验,对不合质量要求的不得进行下道工序,通过自检、互检使施工人员互相学习、互相监督、互相促进,从而提高电气工程的质量。
质量文件是质量体系的运行依据,质量文件编制的好坏,直接影响着体系的运行效果。技术资料务必客观、准确地反映工程施工的内在质量,内容完整,数据准确、真实,签证齐全。电气工程质量的管理应按照先分项工程,再分部工程,最后单位工程的顺序来进行,如建筑工程和建筑设备安装工程共同组成一个单位工程。电气照明工程则属于这一单位工程的分部工程。它又由配管、穿线、上开关灯具、配电盘安装和进户线架设等分项工程组成,开展质量检验工作要循序进行,保证质量文件的准确性,必须实测实量。对检验的部位、项目、计量单位、允许偏差、抽查点数、方法和使用的工具仪表,都要按照规定的标准执行。
电气控制论文篇9
教学程序即课堂教学的组织方法,而教学方法即老师在上课过程中,所采取的具体的授课方式。我们改革了传统的教学方法,实施了教师与学生互动的交互性与灵活性的实践的教学方法,目的是突出学生在实践教学中的主体地位,调动其学习积极性,唤起学生对知识、能力的渴望与追求,具体的实施的教学方法如下:(l)理论与实践并轨教学法。即改革过去大班上课为小班上课,现在每个小班的人数为30人左右,把两个大班分成三个小班,把课堂搬进实验室,采用理论与实践并轨的教学法,使学生真正掌握这门课的精髓。通过几年的实践,效果明显。(2)分层递进式教学法。就是使学生由单元到系统,由简单到复杂,由浅入深、循循渐进地进行了实践教学。教师只提出设计要求,启发思路,学生自主设计,独立思考。(3)课外延伸式教学法。如果学生在课内时间没有按要求完成实践内容,必须在课余时间完成,才算整个课内实践内容完成,否则不能验收与签到。(4)巡回指导法。教师巡回指导,发现问题时,针对教学内容,具体问题具体分析,给予适时的启发与指导。(5)竞赛激励式教学法。在各个项目的实施过程当中,利用分组进行对比试验和竞赛,把比赛成绩作为单元考核的一部分,记入最终的学期总评成绩,目的是引导学生主动创新实践,激励学生勤于思考、勇于探索,团结协作。(队总结巩固法。根据各组任务的完成情况,分别归纳总结其注意事项,进一步提高学生对实际问题处理的方法和技巧。(7)层次分组法。教师将学生分组,按知识水平、操作技能将学生分为A、B、C三个层,然后组成2或3人为一组的协作小组,各组中分别包含A、B、C三个层的学生,这样可相互帮助,互相合作,集大家智慧去完成不同层次的任务。(8)层次指导法。即根据具体的项目任务的不同,老师指导学生的方法分为全指导法、半指导法和零指导法。全指导法即布置第一个项目任务的时候,即在任务的驱动下,由老师来启发、引导学生去完成任务,使学生明确了plc控制系统设计的步骤,学会了设计的过程。在下面的项目任务中,教师采取半指导法,学生尝试着独立来完成项目任务,其充分发挥了学生的主观能动性,使学生主动去触摸知识,探索知识,极大的调动了学习的积极性。在最后的项目研究报告中,采取零指导的方法,即整个项目任务包括项目决策、项目计划、项目的实施以及项目的最终检查等,全由学生通过小组讨论、交流来独立完成,其充分体现了教师为主导、学生为主体的原则,在实施过程中,完全体现了讲”、“做”、“练”一体化中学生的“做”和练的过程。
3教学手段
课程的教学要想获得最佳的教学效果,教学实施过程中还要辅以现代化的教学手段,在良好的教学程序设计下和恰当的教学方法的实施的前提下,再辅以现代化的教学手段来辅助教学,会使教学效果更上一层楼。本课程教学实施过程主要通过以下几个教学手段来实现:(l)多媒体课件的制作。采用信息技术教学手段,制作多媒体教学课件,以Flas的形式进行演示PLC系统的控制过程,图文并茂,提纲掣领,易于理解,有效地调动了学生的研究性和探索性学习的积极性。(2)数字化资源。我们自主开发了现代电气控制技术网络辅助教学平台,该网站包括教学指导、教学资源、课程标准、授课计划、教案、学习资源库、参考文献、授课录像等。可以和老师进行在线的交流与探讨,所有的教学资源可在网上浏览和下载,任何学生在任何时候、任何地方都能借助网络自主学习。(3)虚拟仿真教学。本课程在教学中采用了大量的虚拟仿真技术,利用三菱PLC仿真教学软件,学生可以在机房、宿舍、教室等地方进行三菱PLC指令的学习,加快了学习的进度,提高了学习的效率。(4)一体化实训室。我们把课堂建搬进实训室,利用实训室的多媒体教学设备、计算机网络教学资源和实验实训设备,使学生真正做到边学、边做、边练。(5)技能比赛。通过组织学生科技创新、维修电工大赛、PLC技术大赛、机电产品设计大赛等系列活动,丰富了学生课余生活,培养了学生的专业技能和创新能力。
4考核方案设计
模块化教学区别于传统的填鸭式教学的一个重要的特点就是完全废除传统的笔试考试模式,采取单元式评价与综合评价相结合的过程评价,建立了课程评价体系。《现代电气控制技术》课程以学习情境的工作任务为单元,从以「几个方面进行评价:(l)各个项目的完成情况。占学期总评成绩的25%,每个项目都有自己的评价标准,主要从系统的设计的态度、创新性、设计图纸、技术文件的整理等方面及操作的合理性、安全性、软件设计、安装工艺、调试、解决问题的能力、调试结果等方面进行考核。(2)平时成绩考核。占学期总评成绩的25ty0,通过课后作业、课堂讨论、课堂提问、课堂纪律的遵守情况及实训室规则遵守情况来考核。(3)项目研究报告完成情况考核。占学期总评成绩的20%,主要从书写是否认真、项目报告格式是否正确、是否独立完成、内容是否有错误等方面进行考核。(4)答辩。占学期总评成绩的30%,根据提交上来的研究报告,从回答内容是否准确、流利,有无错漏等方面考核。
电气控制论文篇10
【摘要】本文介绍了经济型数控铣床的功能特性及技术指标,阐述了经济型数控铣床改造的工艺要点, 并对X62W铣宋改造进行了简要的电气系统设计, 提出了经济型数控系统是目前我国机械工业发展的方向。数控铣床是一种自动化铣床,数控技术是数控铣床研究的核心,是制造业
实现自动化、网络化、柔性化、集成化的基础。随着制造技术的发展,现代数控铣床借助现代设计技术、工序集约化和新的功能部件使铣床的加工范围、动态性能、加工精度和可靠性有了极大的提高。
关键词:数控技术;X62W万能铣床;SINUMERIC802D数控系统
目 录
摘 要………………………………………………………….( )
第一章 绪 论
1.1 数控机床的概述………………………………………………………( ) 第二章 铣床情况分析及总体方案的选择 2.2 存在的问题……………………………………………………………( )
2.3 电气控制元件的选用…………………………………………………( )
2.4 铣床的主要改造部位说明……………………………………..( )
第三章 步进电动机及其控制系统
3.1 概述……………………………………………………………………( )
3.2 步进电动机的种类及特性……………………………………………( )
3.3 步进电动机的选用……………………………………………………( )
3.4 步进电动机的控制系统……………………………………….( )
第四章 铣床的电气控制设计
4.1 数控装置的选择……………………………………………( )
4.2 伺服系统的选择……………………………………………( )
4.3电气系统设计……………………………………………….( )
第五章 改进意见及总结
5.1改进意见……………………………………………………( )
5.2本文总结……………………………………………………( )
第六章
第一章 绪 论
1.1 数控机床的概述
数控机床和数控技术是微电子技术同传统机械技术相结合的产物,是一种技术密集型的产品和技术。它是根据机械加工工艺的要求,使电子计算机对整个加工过程进行信息处理与控制,实现生产过程自动化。较好地解决了复杂、精密、多品种、中小批量机械零件加工问题,是一种通用、灵活、高效能的自动化机床。同时,数控技术又是柔性制造系统(FMS)、计算机集成制造系统(CIMS)的技术基础之一,是机电一体化高新科技的重要组成部分。
1.1.1数控系统发展简史及趋势
1946年诞生了世界上第一台电子计算机,这表明人类创造了可增强和部分代替脑力劳动的工具。它与人类在农业、工业社会中创造的那些只是增强体力劳动的工具相比,起了质的飞跃,为人类进入信息社会奠定了基础。 1.数控(NC)阶段(1952~1970年) 2.计算机数控(CNC)阶段(1970年~现在)
到1970年,通用小型计算机业已出现并成批生产。于是将它移植过来作为数控系统的核心部件,从此进入了计算机数控(CNC)阶段(把计算机前面应有的"通用"两个字省略了)。到1971年,美国INTEL公司在世界上第一次将计算机的两个最核心的部件--运算器和控制器,采用大规模集成电路技术集成在一块芯片上,称之为微处理器(MICROPROCESSOR),又可称为中央处理单元(简称CPU)。
到1974年微处理器被应用于数控系统。这是因为小型计算机功能太强,控制一台机床能力有富裕(故当时曾用于控制多台机床,称之为群控),不如采用微处理器经济合理。而且当时的小型机可靠性也不理想。早期的微处理器速度和功能虽还不够高,但可以通过多处理器结构来解决。由于微处理器是通用计算机的核心部件,故仍称为计算机数控。
到了1990年,PC机(个人计算机,国内习惯称微机)的性能已发展到很高的阶段,可以满足作为数控系统核心部件的要求。数控系统从此进入了基于PC的阶段。
总之,计算机数控阶段也经历了三代。即1970年的第四代--小型计算机;1974年的第五代--微处理器和1990年的第六代--基于PC(国外称为PC-BASED)。
还要指出的是,虽然国外早已改称为计算机数控(即CNC)了,而我国仍习惯称数控(NC)。所以我们日常讲的"数控",实质上已是指"计算机数控"了。 1继续向开放式、基于PC的第六代方向发展
基于PC所具有的开放性、低成本、高可靠性、软硬件资源丰富等特点,更多的数控系统生产厂家会走上这条道路。至少采用PC机作为它的前端机,来处理人机界面、编程、联网通信等问题,由原有的系统承担数控的任务。PC机所具有的友好的人机界面,将普及到所有的数控系统。远程通讯,远程诊断和维修将更加普遍。
2向高速化和高精度化发展
这是适应机床向高速和高精度方向发展的需要。
3向智能化方向发展
随着人工智能在计算机领域的不断渗透和发展,数控系统的智能化程度将不断提高。
(1)应用自适应控制技术
数控系统能检测过程中一些重要信息,并自动调整系统的有关参数,达到改进系统运行状态的目的。
(2)引入专家系统指导加工
将熟练工人和专家的经验,加工的一般规律和特殊规律存入系统中,以工艺参数数据库为支撑,建立具有人工智能的专家系统。
(3)引入故障诊断专家系统
(4)智能化数字伺服驱动装置
可以通过自动识别负载,而自动调整参数,使驱动系统获得最佳的运行。
1.1.3机床数控化改造的必要性
1.微观看改造的必要性
从微观上看,数控机床比传统机床有以下突出
的优越性,而且这些优越性均来自数控系统所包含的计算机的威力。
1.1可以加工出传统机床加工不出来的曲线、曲面等复杂的零件。
由于计算机有高超的运算能力,可以瞬时准确地计算出每个坐标轴瞬时应该运动的运动量,因此可以复合成复杂的曲线或曲面。 由于计算机有记忆和存储能力,可以将输入的程序记住和存储下来,然后按程序规定的顺序自动去执行,从而实现自动化。数控机床只要更换一个程序,就可实现另一工件加工的自动化,从而使单件和小批生产得以自动化,故被称为实现了"柔性自动化"。
1.3加工零件的精度高,尺寸分散度小,使装配容易,不再需要"修配"。
1.4可实现多工序的集中,减少零件 在机床间的频繁搬运。
1.5拥有自动报警、自动监控、自动补偿等多种自律功能,因而可实现长时间无人看管加工。
1.6由以上五条派生的好处。:降低了工人的劳动强度,节省了劳动力(一个人可以看管多台机床),减少了工装,缩短了新产品试制周期和生产周期,可对市场需求作出快速反应等等。
以上这些优越性是前人想象不到的,是一个极为重大的突破。此外,机床数控化还是推行FMC(柔性制造单元)、FMS(柔性制造系统)以及CIMS(计算机集成制造系统)等企业信息化改造的基础。数控技术已经成为制造业自动化的核心技术和基础技术。
2.宏观看改造的必要性 1.2 课题的目的、设计要求 1掌握数控机床的电气控制功能
2掌握数控机床电气控制原理。
3掌握机床电气设计方法
毕业设计是培养我们理论联系实际,解决生产实际问题能力的重要步骤,它起到了很大的作用。 它通过对机床数控系统设计总体方案的拟定,机床电气控制框图设计、电气元件的选择及电气控制原理图设计,使我们综合运用所学的机械.电子和微机的知识,进行一次机电结合的全面训练。从而培养了我们具有加工编程能力,初步设计计算的能力以及分析和处理生产中所遇到的机电方面技术问题的能力。 一台普通铣床,利用数控装置进行数控化改造。要求机床采用经济型开环数控装置;
1机床电气控制框图设计。
2选择电气控制元器件。
3电气控制原理图设计
4安装调试说明。
第二章 铣床情况分析 X62W万能铣床是一种通用的多用途机床,它可以进行平面、斜面、螺旋面及成型表面的加工,是一种较为精密的加工设备,它采用继电接触器电路实现电气控制。PLC专为工业环境应用而设计,其显著的特点之一就是可靠性高,抗干扰能力强。将X62W万能铣床电气控制线路改造为可编程控制器控制,可以提高整个电气控制系统的工作性能,减少维护、维修的工作量。
一、X62W万能铣床的主要结构及运动形式
X62W型万能铣床的外形结构如图1所示,它主要由床身、主轴、刀杆、悬梁、工作台、回转盘、横溜板、升降台、底座等几部分组成。在床身的前面有垂直导轨,升降台可沿着它上下移动。在升降台上面的水平导轨上,装有可在平行主轴轴线方向移动(前后移动)的溜板。溜板上部有可转动的回转盘,工作台就在溜板上部回转盘上的导轨上作垂直于主轴轴线方向移动(左右移动)。工作台上有T形槽用来固定工件。这样,安装在工作台上的工件就可以在三个坐标上的六个方向调整位置或进给。
铣床主轴带动铣刀的旋转运动是主运动;铣床工作台的前后(横向)、左右(纵向)和上下(垂直)6个方向的运动是进给运动;铣床其他的运动,如工作台的旋转运动则属于辅助运动。 电气控制线路的工作原理如下:
1.工作分析 控制电路的电源由控制变压器TC输出110V电压供电。
⑴主轴电动机M1的控制 1)主轴电动机M1启动前,应首先选择好主轴的转速,然后合上电源开关QS1,再把主轴换向开关SA3扳到所需要的转向。按下启动按钮SB1(或SB2),接触器KM1线圈得电,KM1主触头和自锁触头闭合,主轴电动机M1启动运转,KM1常开辅助触头(9-10)闭合,为工作台进给电路提供了电源。按下停止按钮SB5(或SB6),SB5-1(或SB6-1)常闭触头分断,接触器KM1线圈失电,KM1触头复位,电动机M1断电惯性运转,SB5-2(或SB6-2)常开触头闭合,接通电磁离合器YC1,主轴电动机M1制动停转。 3)主轴变速时,利用变速手柄与冲动位置开关SQ1,通过M1点动,使齿轮系统产生一次抖动,以便于齿轮顺利啮合,且变速前应先停车。
⑵进给电动机M2的控制
工作台的进给运动 在主轴启动后方可进行。工作台的进给可在3个坐标的6个方向运动,进给运动是通过两个操作手柄和机械联动机构控制相应的位置开关使进给电动机M2正转或反转来实现的,并且6个方向的运动是联锁的,不能同时接通。 2)工作台的左右进给运动由左右进给操作手柄控制。操作手柄与位置开关SQ5和SQ6联动,有左、中、右三个位置,其控制关系见表1。当手柄扳向中间位置时,位置开关SQ5和SQ6均未被压合,进给控制电路处于断开状态;当手柄扳向左或右位置时,手柄压下位置开关SQ5或SQ6,使常闭触头SQ5-2或SQ6-2分断,常开触头SQ5-1或SQ6-1闭合,接触器KM3或KM4得电动作,电动机M2正转或反转。由于在SQ5或SQ6被压合的同时,通过机械机构已将电动机M2的传动链与工作台下面的左右进给丝杠相搭合,所以电动机M2的正转或反转就拖动工作台向左或向右运动。
表1 工作台左右进给手柄位置及其控制关系
手柄位置 位置开关动作 接触器动作 电动机M2转向 传动链搭合丝杠 工作台运动方向
左 SQ5 KM3 正转 左右进给丝杠 向左
中 — — 停止 — 停止
右 SQ6 KM4 反转 左右进给丝杠 向右 当两个操作手柄被置定于某一进给方向后,只能压下四个位置开关SQ3、SQ4、SQ5、SQ6中的一个开关,接通电动机M2正转或反转电路,同时通过机械机构将电动机的传动链与三根丝杠(左右丝杠、上下丝杠、前后丝杠)中的一根(只能是一根)丝杠相搭合,拖动工作台沿选定的进给方向运动,而不会沿其他方向运动。
表2 工作台上、下、中、前、后进给手柄位置及其控制关系
手柄位置 位置开关动作 接触器动作 电动机M2转向 传动链搭合丝杠 工作台运动方向
上
下
中
前
后 SQ4
SQ3
—
SQ3
SQ4 KM4
KM3
—
KM3
KM4 反转
正转
停止
正转
反转 上下进给丝杠
上下进给丝杠
—
前后进给丝杠
前后进给丝杠 向上
向下
停止
向前
向后
左右进给手柄与上下前后手柄实行了联锁控制,如当把左右进给手柄扳向左时,若又将另一个进给手柄扳到向下进给方向,则位置开关SQ5和SQ3均被压下,触头SQ5-2和SQ3-2均分断,断开了接触器KM3和KM4的通路,电动机M2只能停转,保证了操作安全。
3)6个进给方向的快速移动是通过两个进给操作手柄和快速移动按钮配合实现的。安装好工件后,扳动进给操作手柄选定进给方向,按下快速移动按钮SB3或SB4(两地控制),接触器KM2得电,KM2常闭触头分断,电磁离合器YC2失电,将齿轮传动链与进给丝杠分离;KM2两对常开触头闭合,一对使电磁离合器YC3得电,将电动机M2与进给丝杠直接搭合;另一对使接触器KM3或KM4得电动作,电动机M2得电正转或反转,带动工作台沿选定的方向快速移动。由于工作台的快速移动采用的是点动控制,故松开SB3或SB4,快速移动停止。
4)进给变速时与主轴变速时相同,利用变速盘与冲动位置开关SQ2使M1产生瞬时点动,齿轮系统顺利啮合。
2.2.存在的问题
X62W型卧式万能铣床的电气控制系统,存在线路复杂、故障率高、维护工作量大、可靠性差、灵活性差等缺点,
这种老式铣床加工效率低、加工精度差已经快被市面淘汰了现在都已经 是自动化时代了这样的铣床影响切割工件的质量,制约着生产。
2.3电气控制元件的选用
利用微机对X62W型卧式铣床的纵、横向进给进行开环控制,纵向脉冲当量为0.01mm/脉冲,横向脉冲当量为0.005mm/脉冲,驱动元件采步进电动机。改造后的机床能完成一般铣削平面、沟槽、轮齿、螺纹和花键轴等加工工艺,并能控制主轴开停变速、刀架转位及一些辅助功能,使加工实现自动化。在设计的过程中要求掌握数控机床的开环步进系统选用原则,数控改造的方法等。数控系统为经济型数控系统。
图2-1为经济型数控系统的结构
图 2-1 经济型数控系统结构
按数控系统的功能水平,可以把数控系统分为高、中、低三档,低档数控系统即可认为是经济型数控系统。
经济型数控系统一般分辩力和进给速度较低、联动轴数少、人机接口较简单。
一、开环数控系统的总体结构
CNC数控系统由以下几个部分构成:
微机,通常包括中央微处理器、存储器、I/O接口等。
进给伺服系统,在开环数控系统中为步进电机伺服系统。
开关量控制及主轴控制,这部分涉及到M、T、S代码的执行。
人机接口和通信接口。
控制软件。
二、数控系统的功能 三、元件的选用
如果机床使用变频器作为主轴驱动单元,在设计电柜时应考虑采取必要的抗干扰的措施。变频器是很强的干扰源(主要是电源干扰和无线干扰)。如果可能,变频器可安装在独立的电柜内。当变频器和CNC必须安装在同一电柜内时,应按下列要求进行电柜布局:
变频器的电源进线和动力出线在电柜内的长度应尽可能短;
变频器的电源线和动力线应单独布线;
CNC的模拟量控制信号应屏蔽,屏蔽应在变频器端接地;
2.4 铣床的主要改造部位说明 强度计算 又F负=Fs+µ(W+F1),数控装置发出一个脉冲后,工作台的位移量L为一个脉冲当量0.001cm,这时电动机转过的角度f=2pqb/360°,代入式(4)得 M=F负L/hf=360°dp[Fs+µ(G+F1)]/2pqbh=167N·cm式中:µ——机床导轨摩擦系数,取µ=0.18 F1——与重力方向一致,作用在移动部件上的负载力,F1=F垂=1.165kN 如果不考虑启动时的运动部件惯性的影响,则启动力矩Mq=M/0.3~0.5,取安全系数为0.3,Mq=556N·cm。对于工作方式为四相八拍的步进电动机,Mmax=Mq/0.707=786N·cm。 步进电动机的最高频率 取横向进给速度最大为Vmax=1m/min,则步进电动机的最高频率为fmax=1000Vmax/(60×dp)=1667Hz。根据以上数据和经验,选用110BFG型步进电动机较合适,该电动机步距角为0.75°/1.5°,最大静转距为800N·cm,最高空载启动频率为1800Hz。齿轮设计(横向) 据步距角qb、滚珠丝杠螺距p、脉冲当量dp,则在步进电动机与滚珠丝杠之间所加的一对齿轮的传动比为:I=Z1/Z2=dp×360°/(qb·p)=0.8,选Z1=48,Z2=60,根据经验,齿轮模数取1.5mm。3 数控系统硬件设计 所用数控系统是SINUMERIC802D数控系统是西门子公司推出的一款经济型数控系,主要由主控制系统和显示系统两部分组成。主控制系统用于控制键盘的输入和输出,工作台在X、Y方向上的超程,侧门关闭,查询,X和Y向步进电动机的相位及主轴正反转等。显示系统用于控制H716501液晶显示器。这两部分都采用了新型的单片机 GMS90C32作中央处理器,它可以与MCS-51系列单片机兼容,具有快速脉冲编程算法,采用了CMOS技术,最高工作频率可达40MHz(本设计采用18MHz),有良好的性能价格比。
第三章 步进电动机及其控制系统
3.1、概述
开环位置伺服系统亦叫步进式伺服系统,其驱动元件为步进电动机。功率步进电动机盛行于20世纪70年代,且控制系统的结构最简单,控制最容易,维修最方便,控制为全数字化(即数字化的输入指令脉冲对应着数字化的位置输出),这完全符合数字化控制技术的要求,数控系统与步进电动机的驱动控制电路结为一体。 此系统与闭环系统相比,他没位置反馈回路和速度反馈回路,因而不需使用位置、速度测量装置以及复杂的控制调节回路,不仅降低了成本,而且与机床配接容易、控制使用方便。图为采用功率步进电动机的开环系统示意图
& nbsp; 开环步进伺服系统结构示意图
3.2、步进电动机的种类及特性
1 、步进电动机的种类
步进电动机是一种用电脉冲信号转换成相应的角位移的执行器。其角位移量与电脉冲数成正比,其转速与电脉冲频率成反比,通过改变脉冲频率就可以调节电动机的转速。如果停机后某些相的饶组仍保持通电状态,则还具有自锁能力。步进电动机每转一周都有固定的步数,从理论上说其步距误差不会积累。
步进电动机的最大缺点在与其容易失步。特别是在大负载和速度叫高的情况下,失步就更容易发生。
但是,最近几年来发展起来的恒流斩波驱动、PWM驱动、微步驱动、超微步驱动及其它们的综合运用,使得步进见动机的高频出力得到很大的提到,低频震荡得到显著改善,特别是在随着智能微步驱动技术的发展,必将步进电动机的性能提高到一个新的水平。它将以极佳的性能价格比,获得更为广泛的应用,字许多领域将取代直流伺服电动机及相应的伺服系统。
目前,步进电动机主要用于经济型数控机床的进给驱动。一般采用开环的控制结构。也有的采用的是步进电动机驱动的数控机床同时采用了位置检测元件,构成了反馈补偿型的驱动控制结构。
步进电动机按其输出扭距的大小,可分为快速步进电动机和功率步进电动机;按其励磁相数可分为三相、四相、五相、六相;按其工作原理可分为磁电式和反应式两大类。
2、步进电动机的主要特性
1)步距角 a 每输入一电脉冲信号,步进电动机的转子所转过的角度成为步距角。步进电动机步距角可按下式来 计算
a = 360/mkz
式中 m -----步进电动机的相数
z------步进电动机转子的齿数 2)静态步距角误差Δa 空载时,以单脉冲输入,步进电动机实际步距角与理论步距角之差称为静态步距角误差。它随步进电动机的制造精度而变化。
3)最大静转距Tmax 当步进电动机不改变通电状态转子不动时,在轴上加一负载转距,定子与转子就有一个角位移,使转子刚刚离开平衡位置的极限转距称为最大静转距,用T max表示。静转距越大,电动机所能承受的外加转距也越大,一般产品技术规格中给出的最大静转距是指在额定电流及规定的通电方式下的静转距。
设有三相步进电动机,其一转距特性如下图。则A相和B相的矩─-角特性交点的纵坐标Tq称为起动转矩。它表示步进电动机单相励磁时所能带动的极限负载转矩。
当电动机所带负载Tl<Tq时,A相通电,工作点在m点。在次点Ta =Tl, 励磁电流从A相切换到B相,而转子在m点位置时,B相励磁绕组产生的电磁转矩是TB>TA,转子旋转。前进到n 点时,TB =TL,转子到达新的平衡位置。显然,负载转矩TL不可大于A 、B两相交点的转矩Tq,否则转子无法转动,产生“失步”现象。不同相数的步进电动机的起动转矩不同,通过计算可得下表的结果
A B C
步进电动机的最大负载能力
4.3 工作原理
由于步进电机是一种将电脉冲信号转换成直线或角位移的执行元件,它不能直接接到交直流电源上,而必须使用专用设备-步进电机控制驱动器,控制器可以发出脉冲频率从几赫兹到几十千赫兹可以连续变化的脉冲信号,它为环形分配器提供脉冲序列。环形分配器的主要功能是把来自控制环节的脉冲序列按一定的规律分配后,经过功率放大器的放大加到步进电机驱动电源的各项输人端,以驱动步进电机的转动。环形分配器主要有两大类:一类是用计算机软件设计的方法实现环分器要求的功能,通常称软环形分配器。另一类是用硬件构成的环形分配器,通常称为硬环形分配器。功率放大器主要对环形分配器的较小输出信号进行放大.以达到驱动步进电机目的。
3.3 步进电动机的选用
合理的选用步进电动机是相当重要的,通常是希望步进电动机的输出 转距大,起动频率和运行频率高,步距误差小,性能价格比高。但增大转距与快速运行存在一定的矛盾,高兴能与低成本存在矛盾,因此在实际 选用时,必须全面考虑。
首先,应考虑系统的精度和速度的要求。为了提高精度,希望脉冲当量小。但是脉冲当量越小,系统的运行速度就越低。故应兼顾精度与速度的要求来选择系统的脉冲当量。在脉冲当量确定以后,又可以以次为依据来选择步进电动机的步距和传动机构的传动比。
步进电动机的步距角从理论上讲是固定的,但实际上是有误差的。另外,负载转距也将引起步进电动机的定位误差。我们应将步进电动机的步距误差、负载引起的定位误差和传动机构的误差全部考虑在内,使总的误差小于数控机床允许的误差。 3.4步进电动机的控制系统
步进电动机由于采用脉冲方式工作,并且各项需按一定的规律分配脉冲,因此,在步进电动机控制系统中,需要脉冲分配逻辑和脉冲产生逻辑。而脉冲的多少需要根据控制对象的运行轨迹计算得到,因此还需要插补运算器。数控机床所用的功率步进电动机要求控制驱动系统必须有足够的驱动功率,所以还要求有功率驱动部分。为了保证步进电动机不失步地起停,要求控制系统具有升降控制环节。除了上述各环节之外,还有和键盘、纸带阅读机、显示器等输入、输出设备的接口电路及其他附属环节。在闭环控制系统中,还有检测元件的接口电路。在早期的数控系统中,上述各环节都是由硬件系统完成的。但目前的机床数控系统,由于都采用了小型和微型计算机控制,上述很多的控制环节,如升降速控制、脉冲的分配、脉冲的产生、插补运算等都可以有计算机完成,使步进电动机控制系统的硬件电路大为简化。图3-1为计算机控制步进电动机的控制系统框图
系统中的键盘用于向计算机输入和编辑控制代码程序,输入的代码由计算机解释。显示器用于显示控制对象的运动坐标值、故障报警、工作状态及编程代码等各种信息。存储器用来存放监控程序、解释程序、插补运算程序、故障诊断程序,脉冲分配程序、键盘扫描程序、显示驱动程序及用户控制代码程序等。功率放大器用以对计算机送来的脉冲进行功率放大,以驱动步进电动机带动负载运行。
计算机控制系统中,除了上述环节以外,还有各种控制按键及其接口电路(如急停控制、手动输入控制、行程开关接口等)和继电器、电磁阀控制接口等。在复杂的CNC系统中,还可能有纸带阅读机接口、纸带穿孔机接口、位置检测元件输入接口、位置编码器及接口等。 选用高速16位(intei8086/8088z8000及MCS-8098系列单片机)和32位微处理器。
适当配置一些如脉冲分配器和细插补运算器等硬件电路,以减轻MPU的负担。
采用多处理器结构。各种任务可分别由不同的微处理器来完成。
图表3-1步进电动机的CNC系统框图
第四章 铣床的电气控制设计
电气改造设计前,要进行充分的技术准备,因为新系统有许多新功能、新要求、新技术,因此设计前应熟悉技术数据,包括数控系统、伺服系统等操作手册、安装调试手册、编程手册等。要对上述数据进行消化、整理、核对,做到思路清晰,层次分明。选择较为先进的专用火焰切割数控装置,稳定可靠的伺服系统,开发编写PLC软件控制程序等。
4.1数控装置的选择
1 数控系统的选择 其中具有免维护性能的面板控制单元(PCU)是整个系统的核心,具有CNC,PLC,人机界面、通讯等功能。802D最多可控制4个数字进给轴和一个主轴,其中主轴既有数字接口,也可通过模拟接口控制。
控制器: CNC功能: 1.控制车床、钻铣床 2.可控制4个进给轴和一个数字或模拟主轴 3.三轴联动,具有直线插补、平面圆弧插补、螺旋线插补、空间圆弧(CIP)插补等控制方式 4.螺纹加工、变距螺纹加工 5.旋转轴控制 6.端面和柱面坐标转换(C轴功能) 7.前馈控制、加速度突变限制 8.程序预读可达35段 9.刀具寿命监控 10.主轴准停,刚性攻丝、恒线速切削 11.FRAME功能(坐标的平移、旋转、镜象、缩放) 操作与显示: 1.带有8个水平软键和8个垂直软键的直观操作 2.对刀及刀具测量,工件坐标系测量,基本坐标偏移 3.MDA方式端面加工 4.程序段搜索运行 5.坐标轴锁定、快速空运行 6.后台编程 7.加工外部程序(通过串行接口) 8.示波器、袖珍计算器、和工件计数器 9.两种语言在线切换 10.16种语言可选择安装 11.在线公英制切换 12.机床坐标系、工件坐标系、和相对坐标系显示 13.加工轨迹实时显示(可辨认快速和加工轨迹) 14.在线帮助 15.有效G功能和M功能显示 16.坐标位置、余程以及各轴速度显示 PLC: 1.采用标准的S7-200编程语言 Micro/WIN 2.梯图编程 3.梯图在线显示
4.PLC远程诊断 5.完全汉化的PLC编程工具随机提供 6.随机提供PLC子程序和用于车床铣床的PLC应用程序实例 7.PLC的处理速度是6000步/24毫秒 8.40个定时器,32个计数器 9.数字输入输出为144 / 96
4.2伺服系统的选择
伺服驱动系统是西门子802D数控系统和铣床之间的中间环节。如果说CNC装置是数控系统的“大脑”,是“命令”的“指挥所”,那么进给伺服系统则是数控系统的“四肢”,是一种“执行机构”。它忠实地执行由CNC装置发来的运动命令,精确控制执行部件的运动方向,进给速度与位移量。
铣床机通过数控系统发出的控制信息,经过伺服驱动系统的放大,驱动伺服电动机,控制割炬运动并完成切割任务。
1. SIEMENS伺服电动机 4.3.电气系统设计
1. IY0接口电路的设计
IYO口的X2003、>[2004、X2005接口电路 MD1451216]&[7]=0000。
2.主控电路的设计
主控电路完成主轴电动机正、反转,制动;冷动泵、润滑泵和液压泵的电动机启停控制。润滑的问隔时问可由MD14510 E3]&[4]设定。图3中,
第五章 改进意见及总结
5.1、改进意见
在本次的毕业设计中,通过对普通铣床的数控化改造,我认为普通铣床的数控 化改造应遵循以下步骤:
1.改造方案的确定
改造的可行性分析通过以后,就可以针对某台或某几台机床的现况确定改造方案,一般包括:
1.1机械修理与电气改造相结合,
一般来说,需进行电气改造的机床,都需进行机械修理。要确定修理的要求、范围、内容;也要确定因电气改造而需进行机械结构改造的要求、内容;还要确定电气改造与机械修理、改造之间的交错时间要求。机械性能的完好是电气改造成功的基础。 确定改造步骤时,应把整个电气部分改造先分成若干个子系统进行,如数控系统、测量系统、主轴、进给系统、面板控制与强电部分等,待各系统基本成型后再互联完成全系统工作。这样可使改造工作减少遗漏 p;最后,我还要深深地感谢默默支持本人完成学业的父母及亲友,感谢他们为我所做出的无私奉献和巨大支持!
谨向所有在本文的完成中给予过我关怀和帮助而在此无法一一提及的老师、同学和朋友致以诚挚的谢意!
第六章 (1)机床数控技术基础 机械工业出版社 主编 王侃夫
(2)数控技术 机械工业出版社 主编 彭晓楠
(3)数控机床及其应用 机械工业出版社 主编 李善术
(4)现代数控机床伺服系统及检测技术 国防工业出版社 主编 白恩远
电气控制论文篇11
PLC的编制
由于为了降低成本,机床厂家选择的泵一般泵都不具有溢流功能,所以泵和电磁阀的配合显得尤为重要,否则可能造成电机的损毁。如何才能保证合适的时序配合?首先,电机运转的时候电磁阀必须有一个打开,由于电机功率或者流量的限制,而且冷却和冲屑不能同时打开,所以这就要求不管是使用冷却功能还是冲屑功能,在泵启动之前,电磁阀应该先打开,在泵关闭之前,电磁阀不能先关闭,以保证泵的安全,及泵出水口与阀之间管路不承受大的压力而且在使用一个功能前必须保证另一个功能是关闭的,并且为了避免操作上的混乱,各自的功能的通断只能通过各自的按键或者M代码控制,不做交叉控制处理。
电气控制论文篇12
当将鼓风机控制方式转到自动控制方式时,鼓风机启动后,鼓风机的运行频率根据调节池的液位变化自动调整变频器的运行频率;调节池液位达到高液位时,鼓风机在工频下运行,当调节池液位达到高液位以前,鼓风机运行频率随液位的变化而变化;为了保证3台变频控制的鼓风机同时自动控制运行频率一致,在液位显示控制仪表输出的4~20mA信号加装一拖二模拟信号隔离器,通过一拖二模拟信号隔离器将频率信号分别传输给每台鼓风机变频器;从而保证了三台风机变频器的运行频率的一致,保证生产稳定运行。系统图及控制箱原理图如图2所示。
3变频器的选型和技术特性
目前市场上变频器的种类较多,考虑到变频器的性价比及公司内部备品备件问题,我公司选用AB生产的PowerFlex750系列的PowerFlex753变频器,其功能强大,易于使用、灵活且适用于各种工业应用特点,维修方便。变频器具体参数为6脉冲,带直流端子;机柜为IP20,NEMA/UL,变频器功率为160kW,额定电压为400VAC;选用风机水泵类变频器;变频器的具体型号为:20F1NC302。变频器控制柜距离风机距离为60m,小于100米,因此没有选用出线电抗器。
4安装调试
为了保证公司生产稳定,3台鼓风机分开单独改造,一台机组改造成功以后,再着手进行另1台鼓风机改造,即保证了生产的稳定,又使鼓风机变频改造工作连续进行,安装调试一次成功。
电气控制论文篇13
从控制原理上来看,VAVBOX有压力无关型和压力有关型两种类型,其控制原理分别如图1、图2所示。压力有关型VAVBOX其控制回路仅具有温度控制环节,通过温度设定值和当前值进行计算,通过末端风阀开度以调整风量,从而改变房间温度。这种结构同风管静压值息息相关,使得系统的超调量和滞后性较大[4]。而压力无关型末端,通过引入风量控制环节(内环),同温度控制环节(外环)共同作用,实现双闭环控制。由于风量的给定值由温度控制环节计算,因此末端风阀的风量输出与风系统管道静压无关,避免房间温度控制超调现象。但是这种VAVBOX会和送风机的控制回路耦合严重,因此对控制算法要求很高。本文通过改进DDC的控制算法,研究压力无关型末端控制器。其功能框图设计如图3所示。由图3可知,压力无关型末端控制器的信号输入主要有:当前风量、房间当前温度、房间设定温度、阀门开度反馈。信号输出为末端风阀开度控制。当前风量:DC0~10V电压信号,接至DDCAI通道,由末端压差传感器提供。房间当前温度:DC4~20mA电流信号,接入DDCAI通道,由温度传感器提供。阀门开度反馈:DC0~10V电压信号,接至DDCAI通道。房间温度设定:本文中,房间温度设定可由房间内温度控制面板设定,也可通过上位机对DDC的RSP端口赋值,远程设定。两种方式均为标准ModbusRTU信号,接至DDC的Modbus通讯接口。末端风阀开度控制:DC0~10V电压信号,由DDCAO通道输出。通过DDC控制逻辑计算后,由AO端口直接输出至风阀。综上,将DDC同VAVBOX相结合,得到其结构如图4所示。
3DDC末端控制器控制逻辑设计与实现
本文所选用的DDC,其控制逻辑设计是由上位设计软件BasPro完成,通过以太网接口将控制逻辑下载至DDC内。变风量空调系统的特点是随着房间负荷变化而调节自身工作效率,从而实现节能运行。由于在工作时会受到很多随机干扰,常规的PID控制器的参数不能够随着系统变化而寻优。更特殊的是,变风量末端控制同送风机的控制回路相互耦合,因此对现场的末端控制器要求抗干扰性强,控制稳定、精度高[6]。故本文选用的是FPID(自适应PID控制模块)结构如图5所示。FPID控制模块具有实现诸多功能的输入端子,在面对随机干扰时,能够快速整定出PID参数,满足当前工况。其数字量输入端子和模拟量输入端子功能如表1、表2所示[7]。由表1、表2可设计如下控制功能:a.手动模式:如果系统为手动模式,即A/M=0时,输出端子OUT的循环为Mop的参数。即OUT的值可由用户定义。b.自动模式:如果系统在自动模式下,即A/M=1时,则通过自动调节控制输出端OUT为控制器计算值。c.冻结OUT值:通过PV端子设置上限值和下限值来保证输出值。如果PV与SP(RSP或LSP)的绝对差值在最大阀值的范围内,则输出OUT为计算所得,直至PV的值超出了最大阀值。此功能为设置房间的最小和最大进风量,避免房间温度控制出现超调现象。由于设置了最小进风量,房间的空气品质也能够得到保证。d.制冷和制热模式切换:当Action=0,DDC执行正向PID控制。即房间设定温度小于当前房间温度,此时控制器处于夏季制冷模式。同理,当Action=1,DDC执行反向PID控制。e.禁止模式:如果EN=0,系统禁止PID调节,OUT的值设为用户自定义。综上,在VAV末端控制器的外环(温度控制)控制器和内环(风量控制)控制器均采用的是上述FPID参数寻优模块,其最终控制逻辑如图6所示。由于FPID控制模块采用的是自适应PID控制,且系统为双闭环控制系统,根据目标函数寻优法可知,不能实现对温度和风量两个控制器参数的同时寻优[8]。需要对两个控制器是否失控进行逻辑判断,即对两个控制器分别进行PID参数寻优。判断逻辑如图7所示。由图7可知,若出现主环(温度控制环节)和副环(风量控制环节)同时失控,则计时器_61和计时器_62的输出端子Q均为1。将与非门运算结果0赋值给温度控制器的A/M(温度寻优控制模块的手动/自动切换)端子,同时将与门运算结果1赋值给风量控制器的A/M端子。简而言之,即先将温度控制器设为手动,先进行风量控制器寻优。待风量控制器整定完毕后,再进行温度控制器的参数寻优工作。综上所述,基于DDC的VAVBOX参数寻优PID末端控制器的工作流程如图8所示。
4变风量末端控制器在暖通空调系统中应用
在完成对DDC控制器的控制逻辑的设计后,利用DDC所带的Modbus接口同BA系统连接,将其DDC变风量末端控制器同VAVBOX结合,通过LabVIEW采集系统工作数据[9],如图9所示。由图9可知,房间设定温度为20℃,房间的实际温度及风阀的开度及实际送风量均能够很好地跟随变化。房间的过渡时间较为良好,温度超调控制在0.3℃之间,因此DDC控制器的实验效果较为理想。在实验过程中,通过引入随机干扰以改变房间的末端负荷,观察控制器的参数自整定效果和房间温度曲线,得到图10。同图6对比发现,由于引入随机干扰改变了房间负荷变化,风量控制器参数随之发生变化,房间的温度也伴有波动,待风量控制器的参数寻优完毕后,其中P=1.5,I=0.05,控制器已能够适应当前工况。如采用传统PID控制,房间温度会在24.5°附近徘徊。由于采用的是参数自寻优PID控制,因此控制器能够适应此时的工况变化,房间的温度能够继续下降。由于实验中所采用的温度传感器和压差传感器的安装位置多为手动布置,空调系统管道及风机已经施工完毕,不能够完全反映房间的状态。加之风量控制器和温度控制器的失调判断标准为工程经验,因而在实验时多有遗憾。如果能有暖通专业配合,选取合适的测量点,重新选取末端风阀,相信控制效果还能做到更好,节能效果也更加明显。